Over the past few years, discussions about the global supply chain’s state, stability, and security have transitioned from board rooms to headlines. Wars, shortages, and a global pandemic thrust this often overlooked but critical element of the modern market into the public eye, shining a light on its functioning and relative susceptibility to disruption. As a result, many manufacturers have sought to improve their supply chain resilience and efficiency through technology investments.
With connected tech behind them, manufacturers have had the chance to explore new supply chain management models: lean, continuous flow, flexible, custom-configured, and more. Perhaps the most versatile among them, the “agile supply chain,” has emerged as a compelling option amid today’s uncertainty, thanks to its focus on flexibility, communication, and holistic improvement. However, building, managing, and maintaining an agile supply chain can be challenging. Here’s what you need to know.
- What is an Agile Supply Chain
- The Data That Drives Supply Chain Agility
- How MES Software Facilitates Agile Supply Chains
What is an Agile Supply Chain?
The primary feature of an agile supply chain is responsiveness. Rather than emphasizing one element of operations over another, the agile model aims to find the optimal middle ground between efficiency, cost, and quality to ensure a business can adjust to market pressures.
The foundation is built on:
- Defined metrics and benchmarks (the criteria by which a manufacturer measures success).
- Continuous operations monitoring (a stream of data for analysis).
- Open communication channels (consistent and transparent information sharing with partners to contextualize performance).
- Strong contingency roadmaps (data-based plans to support fast responses when conditions change).
While it shares some features with other specialized models (like lean, flexible, or custom-configured), agile management emphasizes balance, making it especially useful in high-precision and specialized markets. For example, lean models prioritize waste reduction at every level of the business, making them an excellent choice for cost-cutting. They focus on perfecting just-in-time delivery to reduce overhead costs related to storage and waste due to spoilage. However, the emphasis on low stocking can leave lean operations underwater when demand spikes.
Agile supply chains, on the other hand, may attempt to mitigate waste but are primarily interested in withstanding ebbs and flows in demand. The goal isn’t waste reduction at all costs; rather, it’s as little waste as possible, provided that the business is prepared to pivot. To achieve this, the model encourages managers to step back from individual enterprise operations and consider the supply chain from start to finish. They use supplier, vendor, market, and on-site performance information to account for upstream changes, like material cost fluctuations, delivery hiccups, and equipment or part shortages.
Essentially, agile supply chains are designed to keep up with whatever the market sends a business’s way.
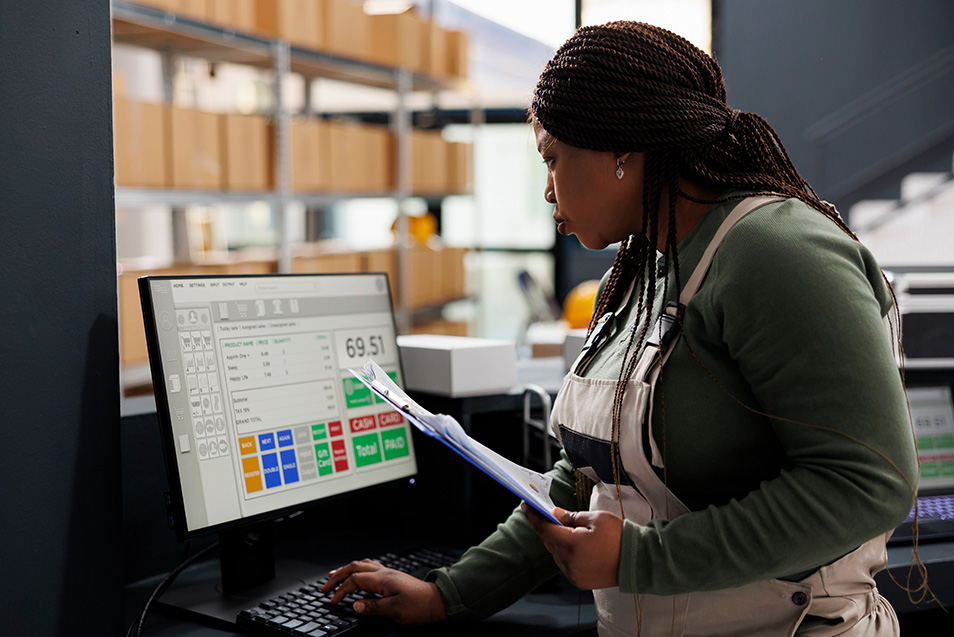
The Data That Drives Supply Chain Agility
Adjusting forecasts and production plans as fluctuations occur is the capability that underlies agile supply chain operations. That means manufacturers pursuing agile supply chain management need accurate, timely data—and lots of it.
Agile supply chains take into account information about variables like:
- Sales history. Every industry has its own supply and demand cycles—and so does each business. Seeing a detailed sales history for your own products can help you better understand seasonal cycles and other patterns, so you’re prepared for the usual ups and downs. Adding real-time data into the mix helps foster agility by ensuring that teams know what you might expect—and any signs that demand is likely to deviate from these patterns.
- Material availability. Demand for products isn’t the only thing that affects performance. Agile supply chains monitor up- and downstream conditions that may affect fulfillment by integrating their operations with those of suppliers, shippers, and buyers can share data from their systems with one another, helping the whole chain—and your factory—run more smoothly.
- Market trends. The labor market, political, and economic pressures can significantly impact demand and production, and their effects may play out in counterintuitive ways. Monitoring real-time indicators of market shifts and the historical effects of similar changes can help manufacturers prepare contingency plans for any number of situations. Should indicators that trends and preferences are changing in ways that might affect your business appear, these systems can raise a flag, so your team has time to respond.
- Facility operations. Having visibility into how things are running on your floor can highlight opportunities to improve processes and accommodate fluctuations. Inventory management, traceability, equipment monitoring, and other operational data provide insight into what’s happening on the floor so teams can make adjustments to ensure fulfillment runs smoothly.
How MES Software Facilitates Agile Supply Chains
Manufacturers have always been acutely aware of the delicate balance that keeps the modern supply chain in working order and how much more complicated maintaining it has become in the era of global operations. Still, the additional scrutiny arising in the past few years has made developing agile supply chains even more critical for these businesses.
In today’s volatile and increasingly interconnected market, demand can change on a dime. Unfortunately, most supply chains can’t do the same. A 2022 study found that while 95% of supply chains experience fluctuations that warrant quick adjustments, only 7% can execute decisions in real-time. That’s where manufacturing execution systems (MES), like TrakSYS™, come in.
These platforms serve as the data and analytics hub for production operations, supporting manufacturers as they define their metrics, monitor performance, interact with partners, and develop contingency plans.
MES platforms make agile supply chain management as simple as possible by:
- Capturing real-time shop floor data. Parsec’s 2023 State of Manufacturing survey found that 42% of North American manufacturers still collect most or all of their data using non-digital processes. Among those who report “completing” their digital transformations, that number drops—but only slightly (31%). Whether through direct integration with business systems and machine assets or in conjunction with industrial Internet of Things (IIoT) devices and specialized sensors, an MES continuously monitors shop floor operations, driving more accurate and impactful data programs.
- Integrating data from various sources. These highly interoperable systems are designed to communicate with other management tools—like enterprise resource planning platforms, client relationship management systems, and warehouse management software—to provide end-to-end visibility into network performance.
- Automating repetitive administrative tasks. In addition to automating data collection, MES platforms can take on production, delivery, maintenance, and fulfillment scheduling, as well as tracking material movement within facilities and other administrative tasks. Without these often-burdensome responsibilities on their plates, team members have more time to focus on higher-value tasks.
- Improving communication. Providing staff with easy access to relevant metrics and insights helps ensure they have what they need to communicate with partners about possible delays, shortfalls, or anything else. This encourages transparency about shipment statuses and strengthens relationships by enabling them to adjust their plans to your performance when needed.
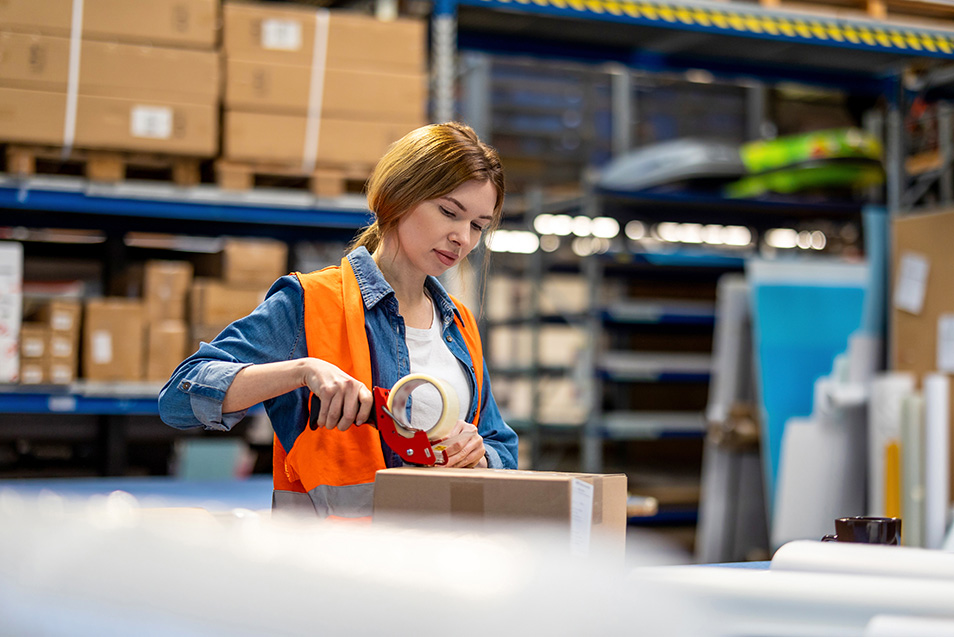
These capabilities ensure the data that drives manufacturers’ decisions is accurate, up-to-date, comprehensive, and accessible to key stakeholders, driving the end-to-end visibility critical to agile operations. To make things even easier, today’s MES systems have the power to do some of the heavy lifting for you by offering:
- Dynamic production scheduling, which uses real-time internal and external data to enable businesses to adjust their schedules to account for things like demand, inventory, asset availability, and other pertinent criteria.
- Data historian features, which can automate historical analyses and benchmarking tasks so you can plan for the future with confidence.
- Real-time reporting dashboards, which offer workers access to their production and supply chain data in ways that work for them.
- Traceability tools, which give insight into material usage throughout production and into distribution, ensuring optimal utilization and enhanced quality control.
- Statistical process control modules, which monitor production processes and use industry standard rules to help teams reduce process variability and standardize quality.
- AI integrations, which ensure you always have access to the emerging tools you need to work seamlessly with partners.
- Visual workflows, which allow your teams to design and configure process automation regardless of their technical know-how.
A robust MES offers advantages across various business roles and activities, from managing manufacturing operations on the factory floor to delivering in-depth analytics for top management. An effective software partner like Parsec will work closely with your team, guaranteeing that your system provides the necessary data, insights, and user experience to maximize flexibility while keeping the intricacies of your business in mind.
To learn more about how MES platforms support manufacturers’ journeys to more responsive, flexible, and agile operations, check out our MES-powered supply chain infographic—and to get started on your journey, contact us today.