Manufacturing operations are a ballet of processes that must operate in concert to avoid production delays, ensure reliable inventory control, and, ultimately, deliver products to customers. Computerized systems have made it possible to collect massive amounts of error-free manufacturing analytics and store it securely for future use, granting manufacturers better visibility into their processes.
Many modern factories use real-time analytics, captured from various physical and digital sources, to monitor their overall production. Gathered insights can encompass things like ingredient inventory, machine performance, uptime and downtime metrics, temperature, vibration rate, and more.
Given the wealth of information that real-time analytics can provide, companies may believe they have everything they need to drive lasting success and improvement. However, what they don’t have is the context surrounding all the data being captured. With real-time analytics, a meter can detect and share a machine’s vibration rate, for instance, but it can’t evaluate the vibration rate in relation to historical performance. The captured data cannot guide manufacturers toward resolving any perceived dips in performance or enable them to implement process improvements that would see equipment operate even more efficiently. Indeed, real-time analytics readily answer the question, “What is happening on the shop floor,” but they cannot provide an answer to the equally as important question of “So what?”. This is where a Manufacturing Execution System (MES) comes into play.
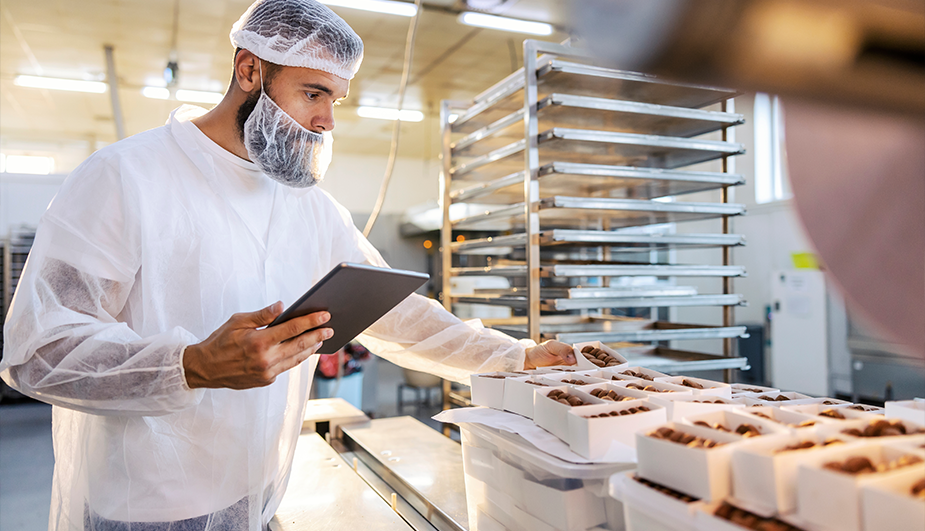
An MES like TrakSYS™ interprets and contextualizes a facility’s data so business leaders can take appropriate action. While a real-time analytics system could certainly inform a Plant Manager of, say, a 45-minute production delay, an MES would do that and more, enabling detailed, root-cause analysis, shedding light on what the immediate next steps are, and how the delay can be avoided in the future. An MES not only manages the collection and analysis of data, but further helps optimize operations, fortify supply chains, and reduce costs. With real-time, contextualized information and straightforward visuals, an MES surpasses mere data capture, providing the framework necessary to benchmark and manage continuous improvement initiatives.
Implementing an MES—even for organizations that already employ real-time analytics—can lead to enterprise-wide improvements ranging from things like increased operational efficiency, reduced downtime, and streamlined performance.
Use Cases for Integrating Manufacturing Analytics With an MES
Integrating an existing real-time analytics solution with an MES helps set the stage for a thriving operation:
Optimized Production Processes
- RTA alone: Capture data around inventory levels, current asset performance, ongoing malfunctions, and finished good counts.
- RTA + MES: Adjust production schedules algorithmically based on things like customer demand, inventory levels and ordering schedules, asset availability, and historical performance; synchronize with an ERP to assign and create jobs, helping optimize labor and resource management; define and configure standard operating procedures to ensure consistency in production.
Quality Enhancement and Defect Reduction
- RTA alone: Support quality management by tracking product defect counts.
- RTA + MES: Provide insights into the root causes of defects, giving teams the ability to remedy issues and improve production processes; use statistical process control to monitor and standardize quality; eliminate recurring problems by flagging any production dates, shifts, products, batches, lots, or lines associated with defects.
Resource Utilization and Optimization
- RTA alone: Monitor finished good counts and compare them to production targets.
- RTA + MES: Gain the insight necessary to abate production bottlenecks and delays; implement process improvements and fine-tune SOPs to ensure consistent production.
Predictive Maintenance and Equipment Longevity
- RTA alone: Capture things like machine states (running, not running), speeds, vibration levels, temperature, etc.
- RTA + MES: Enable predictive maintenance, minimizing equipment downtime and maximizing production capacity; empower maintenance departments by ensuring repair parts are on hand, reducing wrench time and overall maintenance costs; extend equipment life and maximize ROI on existing capital expenditures.
Compliance and Risk Mitigation
- RTA alone: Monitor inventory levels and note when consumption occurs.
- RTA + MES: Provide real-time, complete traceability for both raw materials and finished goods; automate recordkeeping to adhere to regulatory requirements; create comprehensive audit trails, reduce errors, and bolster customer safety and brand reputation by making it possible to rapidly identify the need for and address product recalls.
Visualizing Success
Real-time analytics are undeniably useful for manufacturers, but they are only one piece of the puzzle. Without actionable context, real-time visibility doesn’t give manufacturers the ability to affect positive change. By tying their existing analytics tool into an MES, businesses can maximize the value of their previous investment while simultaneously gaining a detailed record of their operational past, and a contextualized roadmap to their future successes. Through harnessing the power of real-time data and the enterprise-encompassing functionality of an MES, manufacturers can not only remain competitive but thrive in an increasingly complex and fast-paced landscape.