A Defining Component of Effective Quality Management
Quality by the Numbers
Statistical Process Control (SPC) is a vital aspect of quality management within manufacturing. With its ability to help businesses stabilize and enhance the quality of their goods and processes, reduce scrap and rework, and optimize utility consumption, SPC—and its mathematical approach to data analysis—is a pivotal part of any successful quality management program.
The Thresholds of Success
At its core, SPC is about understanding and managing process variation. It’s about recognizing that, while some variation is natural (common cause), other types (special cause) can disrupt process continuity. Establishing process stability is crucial where SPC is concerned, and this is done by setting Upper Control Limits (UCL), Lower Control Limits (LCL), and Center Lining (CL). Once stability is achieved, the focus shifts to ensuring production process variability aligns with customer-defined specification limits, all of which help establish reliable, repeatable quality.
Knowing your Limits
In addition to things like UCLs, LCLs, and CL, Statistical Process Control sees manufacturers focus on several other objective measurements, two of which are the Voice of the Process and the Voice of the Customer:
- Voice of the Process (VoP) is the objective measure of a manufacturing process’s performance. It’s about interpreting what the process data—like cycle time and defect rates—communicates. Monitoring those data points not only helps businesses establish their UCLs and LCLs but also helps them track process stability and identify areas of production that are ripe for improvement.
- Voice of the Customer (VoC) is about aligning manufacturing outputs with customer expectations for quality and performance. It involves gathering and analyzing customer feedback to ensure the product not only meets technical specifications but also fulfills customer needs and preferences. Additionally, Upper Specification Limits (USL) and Lower Specification Limits (LSL) are typically set to provide visibility to the customer preference.
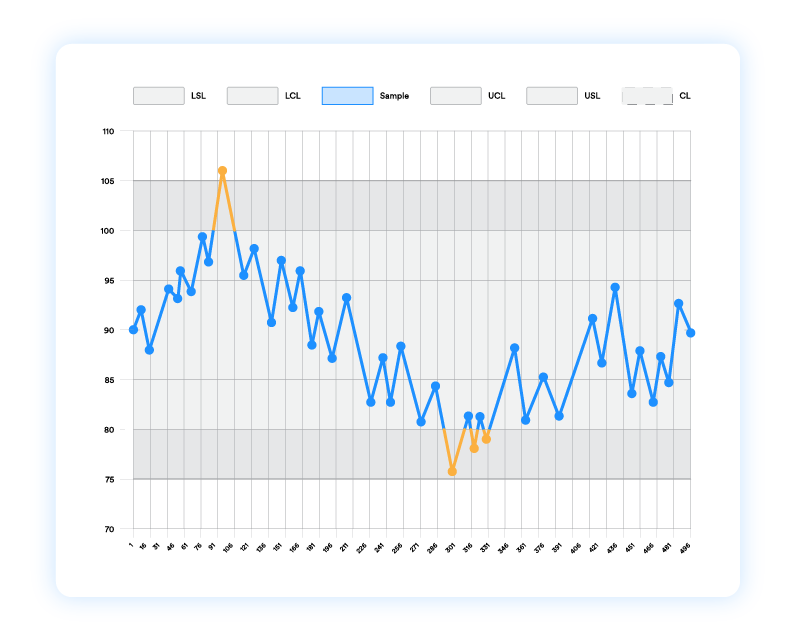
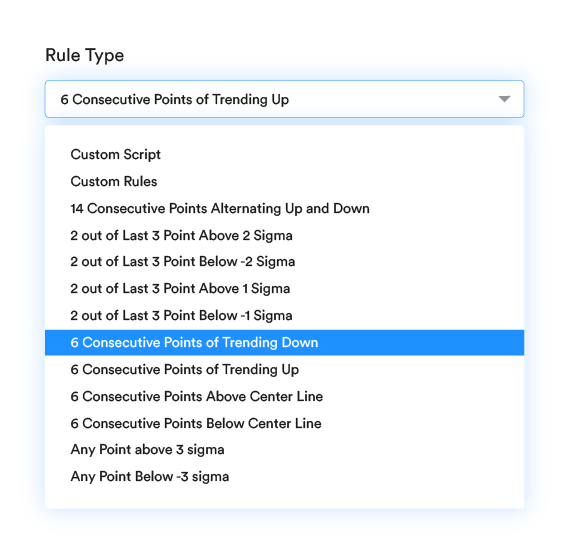
SPC and MES
When paired with a comprehensive manufacturing execution system (MES) platform like TrakSYS, SPC transforms manufacturing quality management. This partnership not only lends additional, pertinent operational context through which to view SPC data but also streamlines the alignment between internal performance benchmarks and customer quality expectations. Whether it be through direct integration with business systems and equipment or through the use of the versatile TrakSYS Smart Devices, when the platform is monitoring production, production team members will instantly be notified when something goes out of spec and will be able to quickly resolve the issue by leveraging the situational context TrakSYS provides.
FAQs
What is SPC?
Statistical Process Control (SPC) is a cornerstone in manufacturing quality management, using data analysis to stabilize and improve product quality, reduce waste, and optimize processes.
Types of Process Variation?
Process variation comes in two types: common cause (natural, inherent variation) and special cause (unexpected, disruptive variation).
What is Process Stability?
Process stability is achieved when a process consistently operates within set Upper Control Limits (UCL), Lower Control Limits (LCL), and Center Lining (CL), indicating predictable and controlled performance.
What is Center Lining?
Center Lining is the concept of adjusting and maintaining the process to run as close to the center (or target value) of its specification limits as possible. The key steps in center lining include:
- Identifying Critical Process Variables: These are the factors that have a significant impact on the output quality or performance of the process. They could be related to materials, machines, methods, or the environment.
- Determining the Optimal Settings: Through experimentation or historical data analysis, the best settings for the critical variables are determined. These settings are where the process performs at its best in terms of quality, efficiency, and output.
- Standardizing the Process: Once the optimal settings are identified, they are standardized across the process. This involves creating guidelines, procedures, and controls to ensure that the process operates at these settings consistently.
- Continuous Monitoring and Adjustment: The process is continuously monitored using SPC tools like control charts. When variations from the center line are detected, adjustments are made to bring the process back to its optimal settings. This might involve recalibrating equipment, adjusting inputs, or retraining operators.
What’s the Difference Between the Voice of the Process and the Voice of the Customer?
Voice of the Process (VoP) is the objective performance data of a process, while Voice of the Customer (VoC) represents customer expectations and feedback on product quality.
How Does SPC work with MES?
Integrating SPC with a comprehensive MES like TrakSYS enhances quality management by providing deeper operational context, aligning performance benchmarks with customer expectations, and ensuring immediate response to specification deviations.