Quality is a term that can be vague or precise, minimal or powerful. Every consumer wants to buy it, and every brand wants to be known for it. Quality products and services are an intrinsic expectation that shapes the value proposition for nearly every organization across the world.
The basic definition of quality – “level of excellence” – hasn’t changed over the years. The parameters for implementing and measuring quality, however, have dramatically transformed since factories first opened their doors in the 1700s to usher in Industry 1.0; and by default, Quality 1.0. Back then, worker productivity and production volume superseded the importance of quality assurance and favorable work conditions.
Starting in the 1940s, technological innovations both increased worker productivity and reduced human participation while enabling continuous improvement practices through standardization. Quality was promoted to an operational requirement, and a plethora of industry standards were created and folded into the cost and way of doing business.
Fast-forward to the mid-1990s and the dawn of Quality 4.0. Terms such as “adaptive” and “augmented” made their way into the industrial lexicon, with organizations modernizing their operations through various paths of digital transformation. As process automation has continued to gain traction, so too have opportunities for elevating human intellect and interaction through diversity and upskilling. Quality mandates and measurements are continuing to make their way up the process chain, supported by holistic methodologies such as ESG (Environmental, Social, and Governance) that help drive employee engagement and quality through a more human-centric lens.
Table of Contents
- What is Quality 4.0?
- What is Manufacturing Quality Management?
- Quality 4.0 and AI (Artificial Intelligence)
- TrakSYS Quality Management System
- Challenges and Opportunities for Implementing Quality 4.0
What is Quality 4.0?
So what exactly is Quality 4.0 today? Aside from a coined phrase for the latest chapter of the ongoing industrial revolution, Quality 4.0 is about harnessing the technologies of today to manifest the future of organizational excellence. It embodies human and artificial intelligence in a way that can propel continuous improvement and accelerate performance across organizations, both for the people they employ and the customers they serve. It unites Industry 4.0 giants such as machine learning, predictive analytics, IoT, big data, and cloud computing with traditional quality management systems.
What is Manufacturing Quality Management?
Manufacturing quality management covers an alphabet soup of standards, strategies, systems, and metrics; from Acceptance Number (the allowable number of defects in a sampling lot) to Work In Process (items that have gone through a manufacturing operation and are now waiting for the next step). Antiquated quality management systems, however, have hindered manufacturers’ ability to effectively adapt and leverage these processes and supporting tools.
In the pharmaceutical industry, for example, manufacturing operations are inherently complex. Implementation of modernized quality management practices is business-critical to ensure products and services meet ever-changing regulatory compliance and consumer safety protocols. The same is true for the food and beverage industry, which also requires strict governance in monitoring and controlling the handling of each ingredient in every step of the production process.
Quality is a holistic endeavor that affects all parts of the business, including workplace compliance, risk management, product assurance, consistency, and innovation. When quality management processes and support tools are deployed within a 4.0 digital transformation, organizations can establish and measure continuous improvement not only across the production line but throughout the enterprise. For example, companies can collect data to identify, rectify, and predict issues; reduce waste; and mitigate quality losses in real-time. Digital tools also enable workers to do their jobs faster, better, and at a reduced cost.
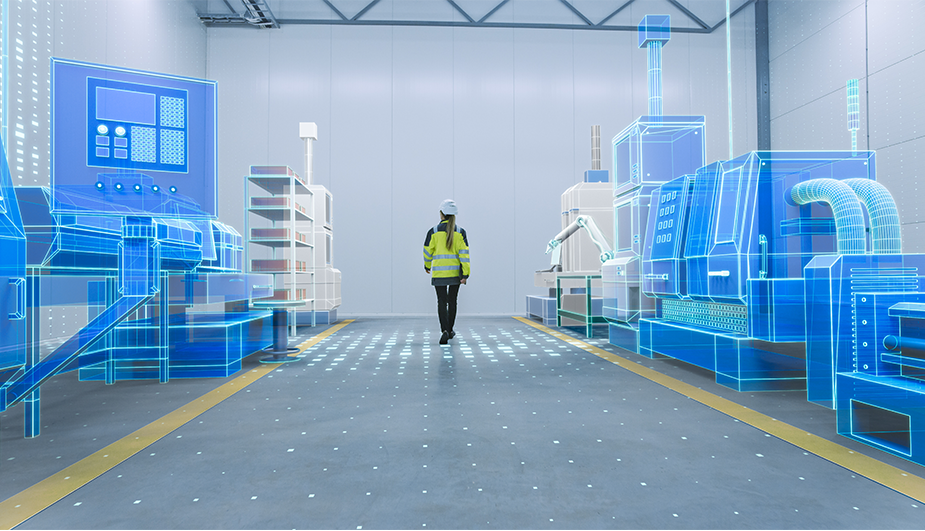
Quality 4.0 and AI (Artificial Intelligence)
The aim of Quality 4.0, and smart manufacturing as a whole, is to leverage emerging tech to make sense of numerous data points collected during production. Artificial intelligence (AI) plays a crucial role in providing the ability to analyze large volumes of both historical backlogs and real-time data and detect patterns and/or anomalies that may cause a lapse in quality. By leveraging advanced analytics, automation technology, and IIoT smart devices, manufacturers can achieve greater efficiency and resilience for lasting impact.
TrakSYS Quality Management System
Parsec makes the management of manufacturing quality as simple as possible with the TrakSYS MES. As an integral part of digitalizing manufacturing operations, TrakSYS manages the collection, analysis, and visualization of data. TrakSYS integrates with existing infrastructures to provide historical trending, SPC (statistical process control), and scrap and defect tracking. The TrakSYS Data Historian records and retrieves time-series production and process data and further enhances TrakSYS Traceability to allow manufacturers to make real-time decisions rather than manually sift through data.
With real-time SPC Analysis, the TrakSYS Smart Data Collection System tracks product and process measurements in real time. When quality loss is detected, the operator is immediately notified so that adjustments can be made quickly to improve process capabilities and minimize the costs of poor quality.
TrakSYS Scrap & Defect Tracking provides visibility and notification of events requiring attention on the plant floor, enabling operators to eliminate processes that contribute to waste production, reduce raw material costs, and bolster sustainability initiatives.
Having access to data is just one part of the equation. TrakSYS also provides a broad range of quality control functions such as preventative action and hazard analysis control, enabling operators to address nonconformances and meet regulatory requirements. Comprehensive E-records provide access to data related to any job, whether it is in process, schedule, or complete, including KPIs, material consumption, and process deviations. Quality dashboards can be configured to suit the exact requirements of an operation. TrakSYS completes the equation to provide a comprehensive, closed-loop system for total manufacturing quality management.
Challenges and Opportunities for Implementing Quality 4.0
Each phase of the quality movement experienced growing pains, and 4.0 is no different. Fluctuations in the economy and consumer behavior push and pull at manufacturers’ priorities and resources and impact the pace and advancement of the manufacturing industry as a whole.
Potential resource challenges may also stem from internal resistance, starting at the top. Lack of alignment between leadership and workers may hamper implementing a culture of quality. Quality leaders may be unclear about how to create value with the processes and technologies at their disposal. Additionally, there may be a lack of analytical and data skills which may pose a significant impediment to implementing Quality 4.0.
Establishing a Quality 4.0 culture is akin to driving a culture of learning in which leadership support, communication, and cross-functional sharing of insights and processes are key. Practicing open communication and fostering a passion for sharing helps to drive employee engagement and adoption. Implementing digitalized technology and tools that make the management of manufacturing quality as simple as possible empowers workers to strengthen their skills, boost productivity, and help scale the organization for continuous improvement and success. Organizations that prioritize operational resilience can successfully address these challenges and embrace Quality 4.0 by augmenting their existing technology and resource assets with the implementation of quality management systems such as TrakSYS.
Quality 4.0 augments traditional quality management systems with digital technologies to enable data collection and insight for continuous improvement across the enterprise.
Quality 4.0 enables manufacturers to collect, analyze, visualize, monitor, and act upon critical operational data in real-time.
Artificial Intelligence helps manufacturers to “make sense” of numerous data points collected historically and in real-time to proactively detect and predict issues that impact quality.