For decades, American manufacturers have been taking production overseas in an effort to cut costs. For a time, the strategy of offshoring was a successful one: companies were able to increase their margins by saving on things like labor and production.
However, the offshoring model is not without its drawbacks. Presently, as manufacturers—across industries—continue to face disrupted supply chains and ongoing labor shortages, the viability of the offshoring model has started to crumble. As a result, many businesses are shuttering their outsourced outfits in favor of more localized operations.
Table of Contents
The Basics
In today’s macroeconomic climate, labor savings aren’t always enough to offset the increased costs of international operations. Over the last five years, inflation and materials shortages have seen the cost of everything from labor to energy, shipping options, and more skyrocket.
As a result, many enterprises are rethinking their global operations—but that doesn’t mean they’re bringing production back to their own zip codes, which are often in high-cost urban centers (reshoring).
Most often, they’re opting for something in between offshoring and restoring:
- Nearshoring refers to the process of relocating production to a low-cost country that is geographically close to (and ideally in the same time zone as) the operations base.
- Onshoring speaks to the process of relocating production to a low-cost city or region in the same country as the operations base.
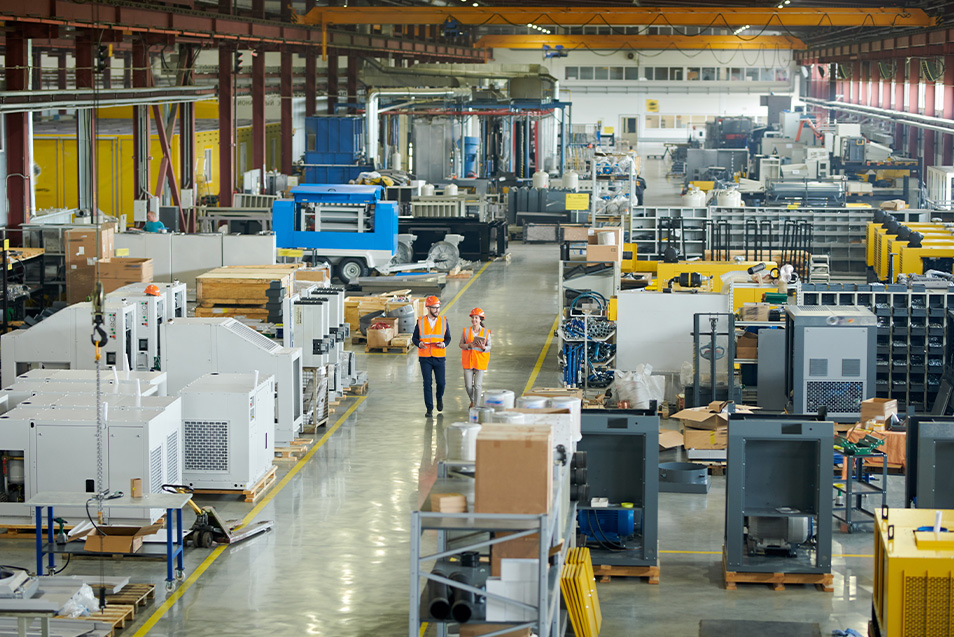
The Benefits of Bringing Production (Near) Home
Bringing production to nearby countries or regions with lower operational costs helps manufacturers balance labor and materials spending with supply chain risk reduction to increase stability. This results in:
-
Lower operational costs
. While traditional offshoring prioritized labor and facility management costs over all other areas, nearshoring and onshoring take a more balanced approach. While labor in nearby nations may cost more than in traditional offshoring choices (like China or Vietnam), manufacturers that relocate closer to home often see logistics, energy, transportation, and other operational costs drop in turn. More resilient supply chains
. The more steps involved, and the farther products or materials must travel, the higher the likelihood that something will go wrong. Keeping operations close to each other and to customers mitigates the risk of large disruptions (like the Ever Given in the Suez Canal or a hurricane in the Bahamas) affecting budgets or reputations.More agile operations
: Though the ability to work with anyone anywhere in the world has led to incredible innovation, proximity breeds expediency and agility. When everyone works the same hours and in nearby locations, manufacturers see response times shorten, time-to-market decrease, operational changes happen faster, and cross-functional collaboration rise.Better quality control
: When quality-related concerns arise, time is of the essence. Waiting until tomorrow morning on the other side of the globe to execute a plan can compound losses by extending downtime, adding to scrap, and wasting energy and team member hours. When everyone is working on the same schedule, businesses are more responsive when quality mishaps occur.
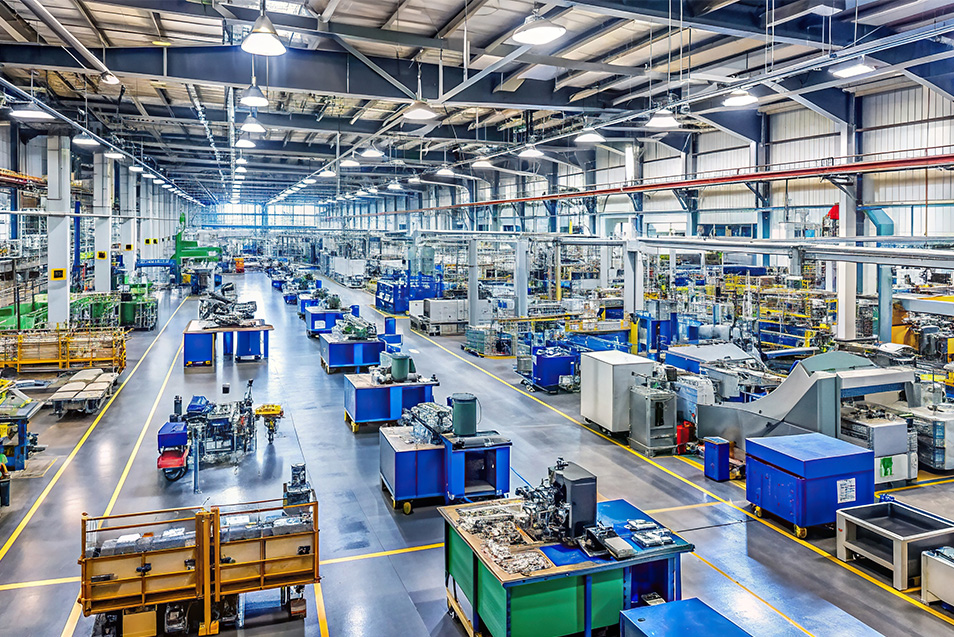
Change-related challenges
Of course, any large-scale change comes with its own set of challenges. Companies considering moving their production processes should plan for:
Higher labor costs
. As noted above, relocating outside of the lowest-cost regions may indeed lead to a bump in labor costs, which can seem a daunting line item to overcome. However, savings in other areas often more than make up for this increase over time. Additionally, companies that choose to onshore their production processes—like many auto manufacturers in recent years—often see improvements to the local economy and labor market as a result.Infrastructure gaps.
One of the benefits of offshoring operations to regions like Southeast Asia was the infrastructure. Manufacturers operating in those countries were able to capitalize on the existing factories, readily available utilities, and established transportation routes. This may not be the case for businesses seeking to move their production to emerging regions like Central America.Supply chain adjustments.
Moving from one nation to another can mean rebuilding the supply chain from the ground up. Be it because existing supply chain partners do not have a presence or do not operate in newly selected regions, issues with time zones, or any other variable, leaders relocating their operations need to be prepared to re-evaluate their vendor partnerships and pivot when necessary.
TrakSYS: Your Partner, Anywhere
Despite the challenges today’s manufacturers face around reshoring, modern operations have one significant advantage over their offshoring predecessors: technology.
Enterprises are more connected than ever before, and the data and analytics generated by connected operations can reduce the complexity associated with identifying potential locations, retooling supply chains, and controlling labor spend.
Our manufacturing execution system (MES), TrakSYS™, can help leaders during this process by:
- Automating data collection and analysis to ensure reports accurately reflect operational performance and models are fine-tuned to the enterprise’s unique business needs so leaders have a true sense of the move’s impacts.
- Using automation and machine learning integration to reduce labor demand in regions that may not yet have established talent pools.
- Boosting production efficiency to mitigate relocation-associated overhead.
- Promoting site-by-site collaboration and innovation by establishing enterprise-wide visibility, knowledge, and control.
- Improving onboarding and training for a new labor force.
As global manufacturing continues to shift from traditional offshoring to nearshoring and onshoring, MES can ensure businesses are prepared to keep up with the challenges of modern supply chains. While the transition poses its own challenges, continuing as usual is likely to be just as challenging in the coming years. That said, the operational efficiency, stability, and positive economic impact nearshoring and onshoring offer present a compelling case for companies willing and ready to adapt.
TrakSYS can help leaders plan their near- or onshoring initiatives with confidence that they’re making the best choice for their company’s present and future—whether they plan to come home, put down roots in a nearby city, or maintain their international presence in a new region.