Manufacturing Operations Management
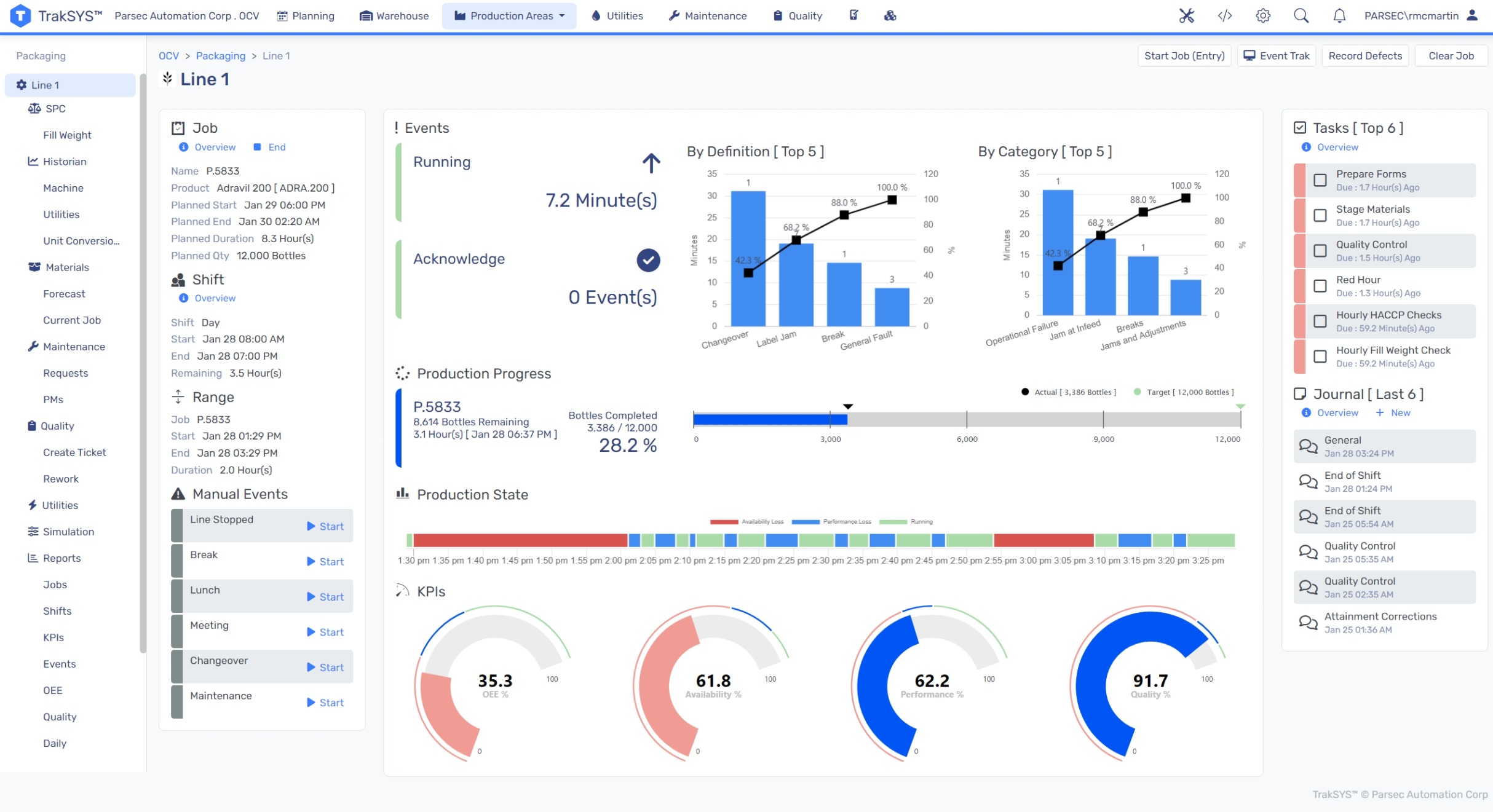
What is Manufacturing Operations Management (MOM)?
Is MOM the same as MES?
Historically, Manufacturing Execution Systems (MES), were focused on automation activities and expanding the locked-down SCADA/HMI Capabilities. This provided flexibility to the manufacturing process by allowing operators to capture expanding event data and visualize that data in real-time. Fast-forward to today and MES platforms like TrakSYS have built out their feature set of capabilities like workflow, SPC, etc.…) to become the go-to software platform for executing and optimizing the principles of manufacturing operations management.
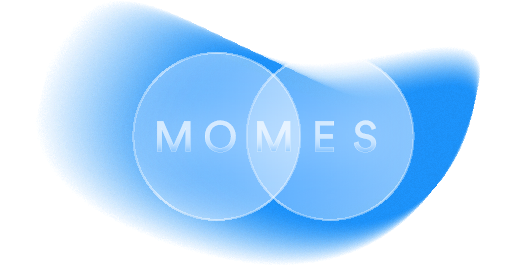
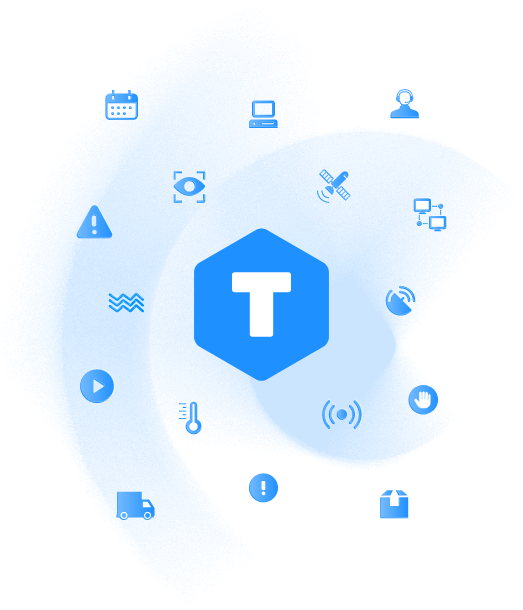
Making System Interoperability as Seamless As Possible
Interoperability is a crucial aspect of Manufacturing Operations Management because it ensures that various systems and technologies within a manufacturing environment can seamlessly communicate and work together. In a typical operation, multiple systems such as ERP (Enterprise Resource Planning), MES, quality management systems, maintenance software, and supply chain management tools are used to handle different aspects of production. For MOM to be effective, these systems must be integrated and interoperable, allowing for the free flow of data and information across the organization.
To enable streamlined interoperability, we created TrakSYS Connect: a feature of our MES platform that is designed to simplify the process of building interfaces between different systems for the type of multilateral data exchange described above. Connect automates many functions (like payload structures and interface types) that previously required extensive coding, making solution creation and delivery more efficient.
Unified Data. Endless Possibilities.
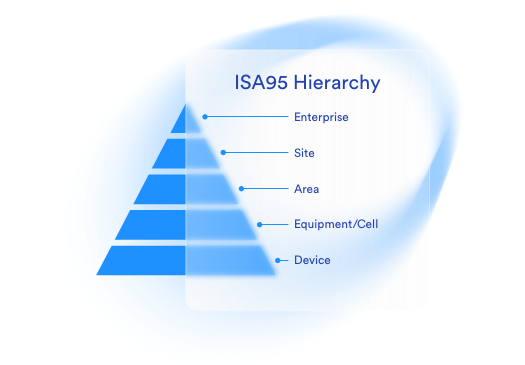
Talk with a Consultant
The Four Pillars of Manufacturing Operations Management
Production Management
This pillar focuses on the planning, scheduling, execution, and tracking of production processes, ensuring that manufacturing activities align with demand, production schedules, and resource availability. Production management helps optimize the use of materials, labor, and machinery, ensuring efficient workflow on the shop floor. It also includes monitoring production progress in real-time and addressing any deviations to meet targets and maintain product quality.
- Enhanced operational visibility: Integrated systems provide real-time data on production processes, allowing organizations to monitor performance, identify bottlenecks, and make informed decisions.
- Optimized resource allocation: By integrating production planning systems with control systems, organizations can optimize the allocation of resources, ensuring that production capacity aligns with demand.
Maintenance Management
Maintenance management is essential for ensuring that manufacturing equipment and machinery remain operational and efficient. This pillar involves both preventive and predictive maintenance strategies to minimize downtime and extend equipment life. By closely monitoring the condition of equipment, the system can schedule maintenance activities without disrupting production, reducing unexpected failures and ensuring continuous manufacturing operations.
- Predictive maintenance: Integrated systems can enable organizations to implement predictive maintenance strategies by analyzing equipment data to identify potential failures before they occur. This can help to reduce downtime and improve equipment reliability.
- Optimized maintenance planning: By integrating maintenance management systems with production equipment, organizations can optimize maintenance schedules and minimize disruptions to production.
Quality Management
The quality management pillar ensures that the manufacturing process consistently produces products that meet or exceed defined quality standards. It involves real-time quality monitoring, in-process inspections, and control procedures to detect and address defects or deviations. Quality management systems in MOM also support compliance with industry regulations and certifications by providing traceability, corrective actions, and continuous improvement efforts.- Improved quality control: Integrated systems can facilitate the integration of quality management systems with production processes, enabling organizations to monitor product quality in real-time and take corrective actions as needed.
- Enhanced product traceability: Integrated systems can support product traceability, which is essential for compliance with quality standards and regulations.
Inventory & Supply Chain Management
This pillar manages the flow of materials and resources throughout the manufacturing process. It includes material planning, procurement, inventory control, and logistics. Effective supply chain management ensures that the right materials are available at the right time to avoid production delays. It also involves managing relationships with suppliers, optimizing inventory levels, and ensuring that finished products are delivered to customers on time, all while minimizing waste and costs.
- Accurate inventory management: Integrated systems can provide real-time data on inventory levels, enabling organizations to ensure that materials are available when needed and avoid stockouts or excess inventory.
- Optimized supply chain management: By integrating inventory management systems with supply chain planning systems, organizations can optimize the flow of materials through the supply chain, reducing costs and improving efficiency.
FAQs
What is Manufacturing Operations Management (MOM)?
What is Lean Manufacturing?
Lean Manufacturing is a systematic approach to improving production efficiency by minimizing waste while maintaining high-quality standards. It focuses on optimizing workflows, reducing unnecessary processes, and enhancing value for customers by eliminating inefficiencies in manufacturing operations.
What is ISA-95?
What is The Difference Between MES and MOM?
What are the Four Pillars of MOM?
- Production Management – Optimizes scheduling, execution, and tracking of production activities.
- Quality Management – Ensures compliance with quality standards and enhances traceability.
- Maintenance Management – Implements predictive maintenance strategies to reduce downtime and extend equipment life.
- Inventory & Supply Chain Management – Ensures efficient material flow and inventory optimization to prevent disruptions in production.