The past decade has seen manufacturing’s digital maturity grow by leaps and bounds. Across industries, companies have made significant improvements to their operations thanks to the enhanced visibility specialized platforms—like Manufacturing Execution Systems (MES)—provide.
By now, it is widely accepted that reliable, comprehensive, actionable data is key to unlocking the aforementioned improvements. As more businesses turn to gathering, correlating, and contextualizing increasing volumes of data, the question becomes: Well, what about storage?
Table of Contents
Best Practices for Better Data Programs
Data collection and management can be an overwhelming and confusing topic, but there are some foundational principles that can guide leaders as they seek to implement effective, efficient data management practices:
Different data is for different things
Though there are countless possible data sets available to manufacturers, most can be categorized into one of four categories.
Purpose | Examples | |
Operational | Gives insight into how the production line is running to ensure leaders understand how different areas of the business connect to one another, guiding more informed decisions | Overall equipment effectiveness (OEE) Maintenance records Production schedules Cycle times |
Quality | Illustrates the consistency and reliability of production process to help manufacturers get ahead of quality concerns to address them in a timely manner | Defect rates Inspection results Yield vs. throughput Unit specifications |
Supply chain | Shows how up- and down-stream variables affect facility operations to help manufacturers avoid production and shipping delays, adjust to materials shortages, and forecast potential supply chain disruptions | Inventory tracking Storage insights Supplier performance Logistics information |
Customer | Provides valuable context about customer histories to show how facility operations may affect buyers and guide service teams toward timely resolutions | Buyer feedback Fulfillment preferences Purchasing behaviors Order histories |
While these categories reflect the most common uses of each data source/set, manufacturers may use these metrics in a wide variety of ways. Additionally, data points from multiple groups may be analyzed side-by-side to reveal information about another “area” of production.
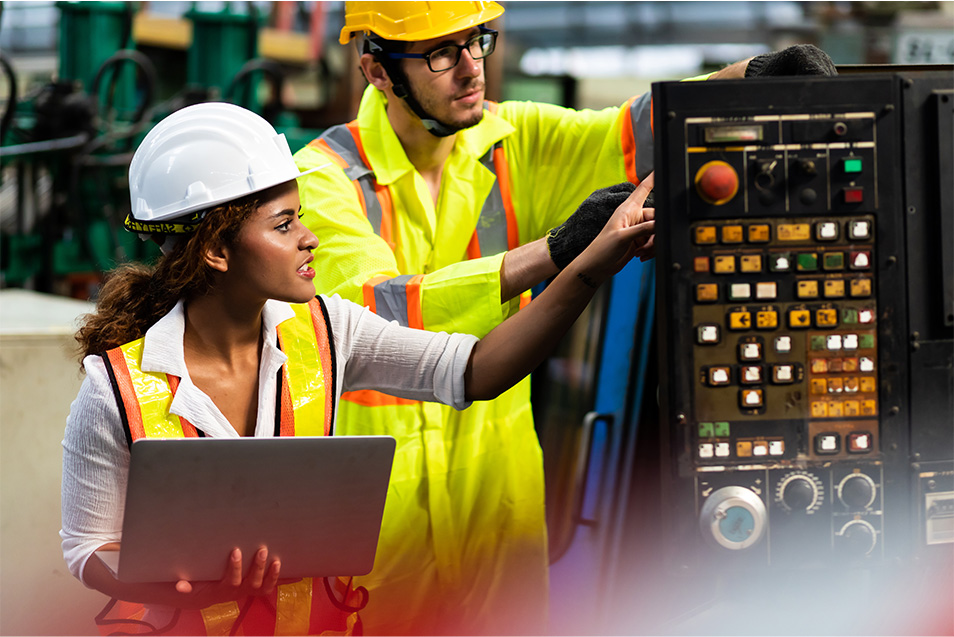
Analytics are only as accurate as the source
To get useful insights and predictions, manufacturers need accurate, reliable, up-to-date data. Though manual collection remains popular, the industry at large is increasingly shifting toward automated data gathering and process monitoring as Inaccurate, incomplete, or inconsistent data sets can quickly skew the reality of an operation’s health.
At the heart of these smart systems are industrial Internet of Things (IIoT) devices, which continuously monitor production processes to log key data points. These capabilities may be native to newer equipment or added to legacy assets to allow manufacturers to engage in data-led practices without needing to refurbish their facilities. In either case, IIoT devices help manufacturers avoid errors in their records, enable continuous monitoring, and offset additional labor demands associated with data collection, thereby freeing workers to focus on other high-value tasks.
Integration unlocks insight
When different facilities, departments, or business areas use different systems, datasets may become siloed from one another, preventing holistic analysis. Because of that, de-siloing data across the enterprise is a critical step for businesses wanting to pursue data-led transformations. Adopting a unified namespace (UNS)—a software layer in industrial automation systems that acts as a single source of truth for all manufacturing data—enables businesses to create an event-driven architecture (EDA) design pattern, something which enables low-latency, real-time data processing.
Alongside those solutions, artificial intelligence, which has many beneficial applications in connected manufacturing, can support data integration efforts by automating reconciliation, maintenance, and record cleaning within a UNS or other central database. Specialized AIs can be trained to continuously review, cross-reference, and correct records to maintain accuracy, avoid redundancy, and drive better results.
Access amplifies results
While optimizing data gathering and storage practices is indeed important, ensuring appropriate access is equally as important. To accommodate this, many MES platforms offer flexible visualization and custom analytics options to ensure that data-based decisions are happening at every level of the enterprise.
Now, it is true that digital systems can come with security risks—especially when they are widely accessible to employees. As such, it is important to strike a balance between making insights available to employees and making physical equipment inaccessible to bad actors. It’s a challenging task for those without specialized expertise. Role-based access controls (RBAC) can help IT/OT managers simplify access management by assigning permissions based on an individual user’s title and responsibilities. This ensures your people have the access they need to do their jobs while helping to safeguard networks against bad actors.
Planning ahead pays off
Fully connected systems generate massive volumes of data, and manufacturers need somewhere to store it all. Since historical data is critical to tracking progress, systems’ storage and processing capacity need to be able to scale alongside their data lakes. Manufacturers need to start planning for this growth on day one, as not all data management models nor computing hardware will be able to scale as quickly as needed.
Terms to know | ||||
Storage/Processing | Data Architecture | |||
On-premises | Servers located on physical premises Low-latency processing/retrieval Harder to scale; limited by physical footprint and hardware specifications More up-front investment in physical equipment | Hierarchical | Represented in a “tree” format Uses simple “parent/child” relationships to organize information Well-suited to complex systems with large amounts of data More efficient processing and navigation | |
Cloud | Servers located in data center(s) More latency due to network connection speed/distance Highly scalable Lower investment (renting capacity rather than buying servers) | Relational | Represented in a table format Groups information based on shared variables and links related groups Easy to scale but often has more latency than other options | |
Hybrid | Some servers on the premises; others in data center(s) Allows for prioritization of high-importance tasks to on-prem servers Middle ground between scalability/speed of cloud/on-prem Must manage two types of systems | Network | Represented in a modified tree format Uses parent/child relationships but allows for the child to have multiple parents Improved retrieval and access speed Relatively inflexible and limited scalability |
Having a backup and disaster recovery (BDR) plan is also critical, as it protects manufacturers from data losses in the wake of a critical system failure. These solutions automatically copy and save duplicates of enterprise records to a secondary location to ensure that critical information isn’t lost when disaster strikes.
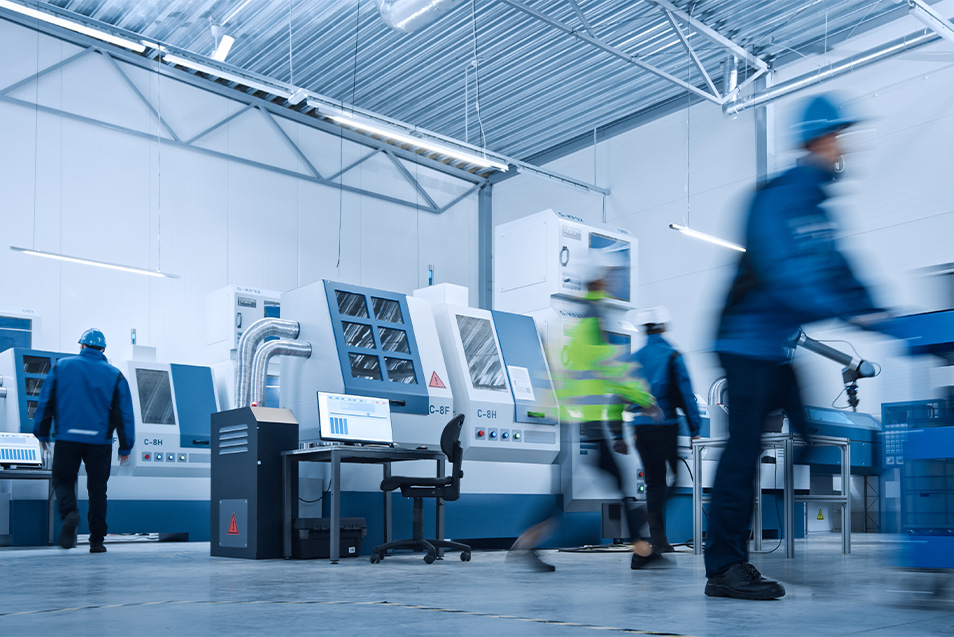
Step by Step: Developing a Data Management Plan
A data management plan is like a project roadmap for data-based transformations. It outlines the business’ data maintenance processes and goals to ensure you have the tools you need to collect, store, integrate, and access this information wherever and whenever your team needs it. As you outline your plan, follow these steps:
- Reflect critically. Audit your current procedures around data management to ensure you have a comprehensive understanding of the facility’s current maturity level. Do research, review records, and commit to critically evaluating your tried-and-true processes. Speaking with a wide range of employees may also be valuable at this stage, as it can give insight into issues or bottlenecks that may not be apparent to leadership but are obvious to the people who engage with production on a daily basis.
- Set clear objectives. Effective organizational changes are driven by outcomes, not technologies. Instead of identifying tools you’d like to use, identify goals you’d like to reach that focus on tangible outcomes—like improving reaction time when issues arise.
- Think big. Now, take a step back. Data management and strategy aren’t just about internal processes. They’re also about your role in the market. As you consider your objectives, let yourself think about the bigger picture. How will your data use set you apart in the market? How will it help you get ahead of the competition?
- Explore solutions. Use the internal and market goals outlined in steps two and three to identify MES options with features that will bring you closer to your objectives. Along the way, keep in mind the key metrics by which you will measure success and seek out tech solutions that will help you track your progress over time.
- Invest in your people. The best data management plans can fall apart when the whole staff isn’t on board. It’s critical that manufacturers invest in education and upskilling for employees, so they understand how to access, use, and interpret data now and are prepared for additional adjustments down the road.
- Keep pushing. While the implementation and deployment phase might end, the work of optimization won’t—and that’s the whole point. Developing a culture of data-driven improvement means accepting that there will also be improvements to make and new ideas to explore.
Still feeling unsure about your data management planning? Parsec can help you get started. To learn more about how TrakSYS has helped manufacturers transform their operations, read our whitepaper or contact us today.