2024 has only just begun, and product recalls across industries—from pet food to massagers to baby formula—are already making headlines. With these unsettling stories capturing news cycles so early in the new year, quality is sure to be a key focus for manufacturers moving forward. That said, achieving efficient, sustainable, and repeatable quality doesn’t come easy, and cost-effective quality management is both an art and a science requiring focused attention and long-term commitment.
The concept of Cost of Quality (CoQ) plays a crucial role in a business’s understanding of the financial implications of ensuring consistently high-quality products. In this blog, we’ll dive into the world of manufacturing CoQ, parse through the Cost of Poor Quality (CoPQ) and the Cost of Good Quality (CoGQ), and unpack CoQ’s utility in today’s digitally evolving manufacturing landscape.
Table of Contents
- What is Cost of Quality?
- Cost of Poor Quality (CoPQ)
- Cost of Good Quality (CoGQ)s
- TrakSYS for Quality Management
What is Cost of Quality?
Cost of Quality is a comprehensive term encompassing the resources expended to both prevent poor quality and ensure good quality in manufacturing processes. The CoQ formula is therefore represented as the sum of Cost of Poor Quality (CoPQ) and Cost of Good Quality (CoGQ).
CoQ = CoPQ + CoGQ
CoPQ can be further divided into internal and external failure costs, while CoGQ can be further divided into prevention and appraisal costs. We explore each of these costs below.
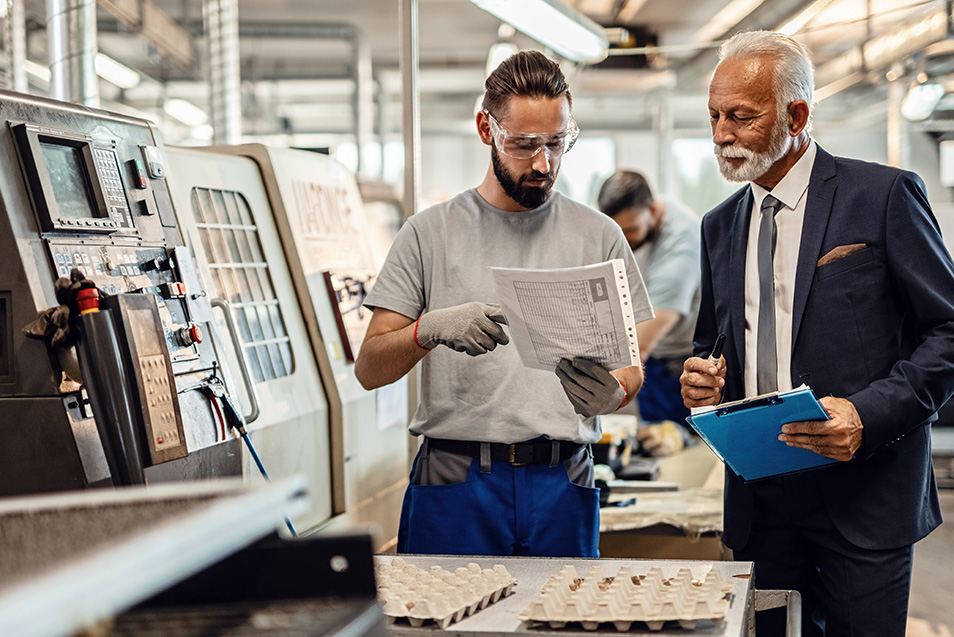
Cost of Poor Quality (CoPQ)
Cost of Poor Quality refers to financial losses that result from poor product quality. Put simply: it’s the amount of money the manufacturer loses on errors and rejected output. There are two components that contribute to CoPQ:
- Internal failure: An internal failure occurs when poor product quality is detected before the product is sent to the customer. This includes the cost of rework, repair, re-testing, internal scrap, failure analysis, and raw or in-process rejects.
- External failure: An external failure occurs after the product reaches the customer. For example, if the product malfunctions after initial use or if the customer communicates the lack of quality to the manufacturer. External failure costs include replacements, warranty claims, compliance penalties, materials, investigations, and potential damage to brand reputation and customer loyalty. After all, external failures are more likely to make headlines than issues caught before shipment. By allowing unsatisfactory or unsafe products to get into the hands of its customers, a business risks losing both their trust and patronage forever—an ominous financial loss that’s difficult to quantify in the long run.
Evaluating CoPQ enables manufacturers to understand the impact of poor quality on profits. Furthermore, through conducting root-cause analysis and identifying the main disruptors to their quality, businesses are able to implement actionable improvement plans aimed at addressing the underlying causalities. In addition to conducting a thorough CoPQ analysis, manufacturers can likewise reduce CoPQ by prioritizing proactive quality assurance measures. Enter: Cost of Good Quality.
Cost of Good Quality (CoGQ)
Cost of Good Quality is a measure of the resources needed to do things right the first time around; it refers to the costs associated with proactive efforts to reduce error and ensure high quality. Like its poor-quality counterpart, CoGQ consists of two components:
- Prevention: Preventative costs are dedicated to avoiding subpar finished goods. These include things like employee training, raw material analysis, supplier evaluation, quality audits, and market research.
- Appraisal: Appraisal occurs when a manufacturer enlists a third-party expert to test products and investigate the causes of poor quality. By focusing on testing, measurement, and auditing, appraisal puts a stethoscope to quality issues, reports on key findings, and ultimately contributes to overall prevention. These costs include payment of experts, production machine and tool calibration, laboratory testing, and various types of inspection.
Prevention is almost always cheaper than cleaning up failures—and it’s better for the business overall. Generally, it’s a good sign if a manufacturer’s investment in ensuring good quality supersedes its investment in remedying poor quality. However, there may still be opportunities to streamline preventative costs—something we dive into in the next section.
With all of the above context in mind, it’s clear that monitoring and managing their overall CoQ is critical for manufacturers who want to strengthen quality and ensure less-than-ideal quality doesn’t hinder long-term profitability or business growth. When manufacturers take control of their CoQ, they can tangibly contribute to larger business objectives.
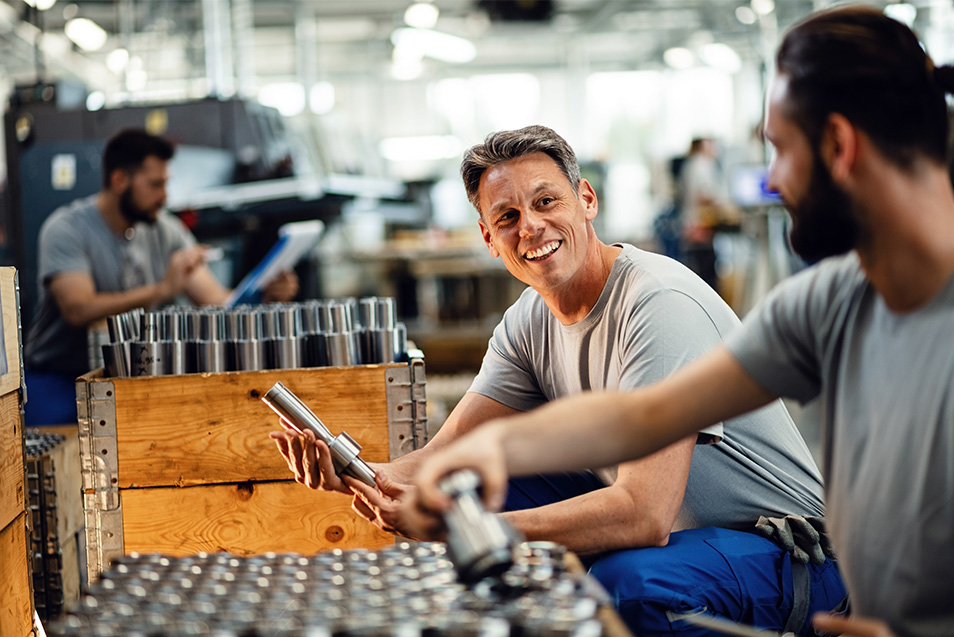
TrakSYS for Quality Management
High quality comes at a premium for manufacturers and consumers alike, but proper CoQ management can help control costs, especially when it’s part of a long-term and comprehensive improvement strategy. Manufacturing execution systems like TrakSYS™ empower manufacturers to take control of their CoQ with real-time data and unparalleled visibility into all essential elements of quality management, including scheduling, equipment efficiency, scrap and reject levels, employee activity, root-cause analysis, and audit trail.
Global market intelligence firm IDC conducted research on the tangible business value of TrakSYS and found that users saw meaningful improvements in both quality and efficiency. The research revealed that, after implementing TrakSYS, clients saw manufacturing errors drop by 28%—and when errors did occur, TrakSYS users achieved remediation 30% faster than before. Moreover, the research found that TrakSYS positively impacted quality control (QC) and maintenance teams’ overall performance, resulting in average annual salary savings of over $375,000 ($165,600 for QC teams and $213,000 for maintenance teams, respectively).
The facts are clear: if a business has yet to optimize CoQ, they are leaving value on the table. TrakSYS helps manufacturers implement systematic approaches to reduce process variation and maximize product quality and compliance, leading to standardized processes, improved customer satisfaction, sustained regulatory compliance, and reduced quality costs.
To learn more about how TrakSYS can help you conquer CoQ, visit our Quality Management page now.