Quality Management
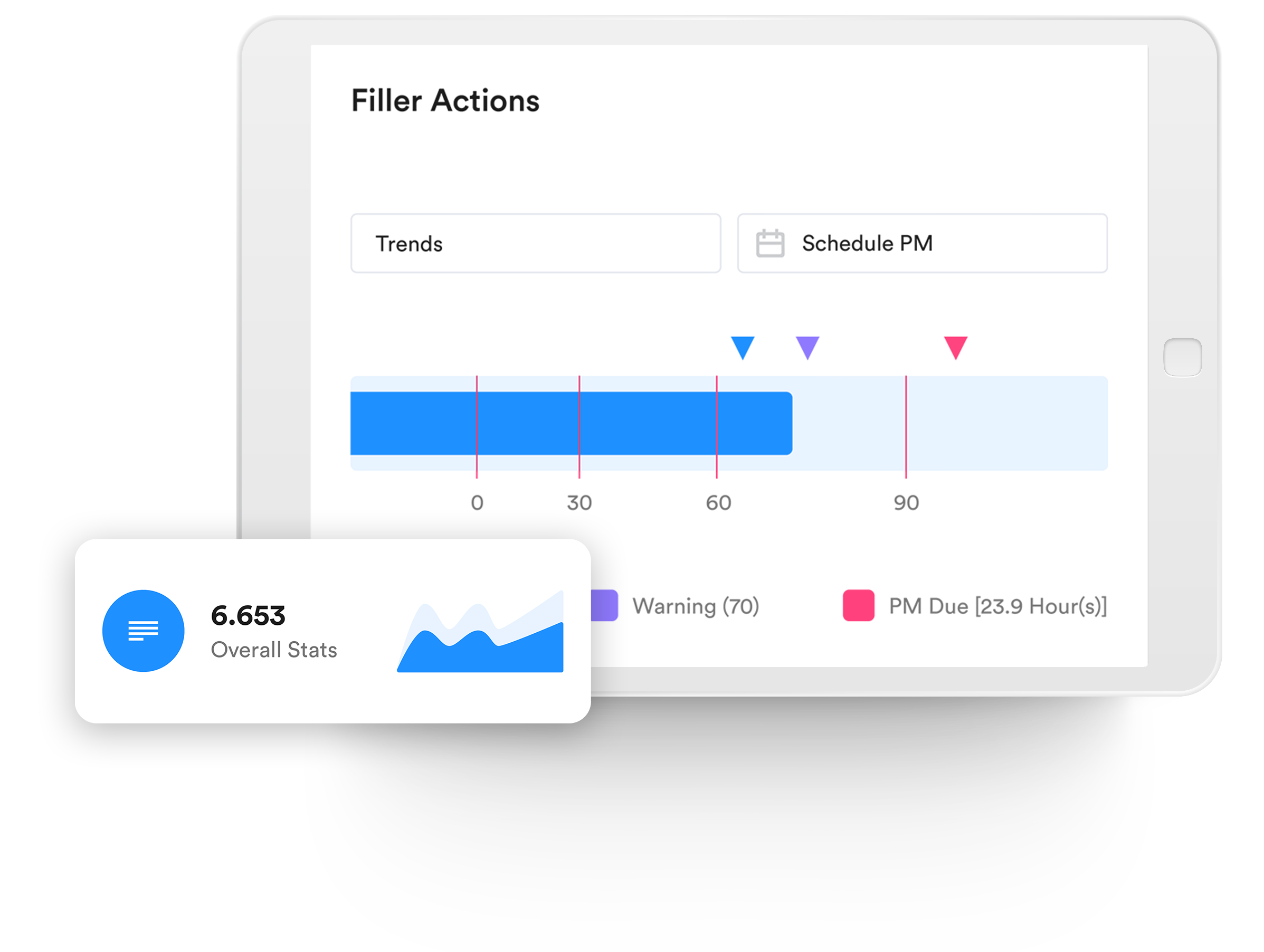
Quality Management Made Efficient, Sustainable, and Repeatable
Through a real-time, interactive, and operationally-focused approach to your quality management system, TrakSYS makes it possible to bring about and enforce a quality-by-design culture that is both effective and sustainable. The availability of real-time, contextualized information using TrakSYS provides deep insights into the causes of poor quality. And TrakSYS provides the tools to take quick action on those insights, creating a closed-loop system of quality management.
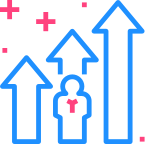
Improve Customer Satisfaction
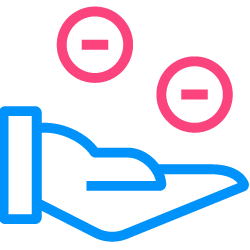
Reduce Costs of Poor Quality
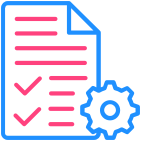
Standardize Processes
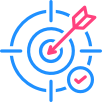
Maintain Regulatory Compliance
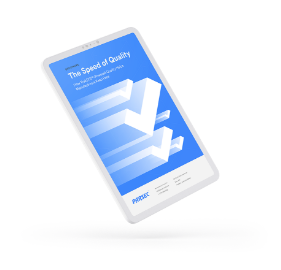
Download the TrakSYS Quality Management Brochure
We’re committed to your privacy. Parsec uses the information you provide to us to contact you about our relevant content, products, and services. You may unsubscribe from these communications at any time. For more information, check out our Privacy Policy.
A Comprehensive Quality Management Solution
With TrakSYS, you can control all essential elements of quality management such as tasks, scheduling, procedures, employee qualifications, reports, and analysis, notifications, and audit trail. Based on an easy-to-use mobile platform, TrakSYS quality management solutions can help you implement systematic approaches to reduce process variation and maximize product quality and compliance.
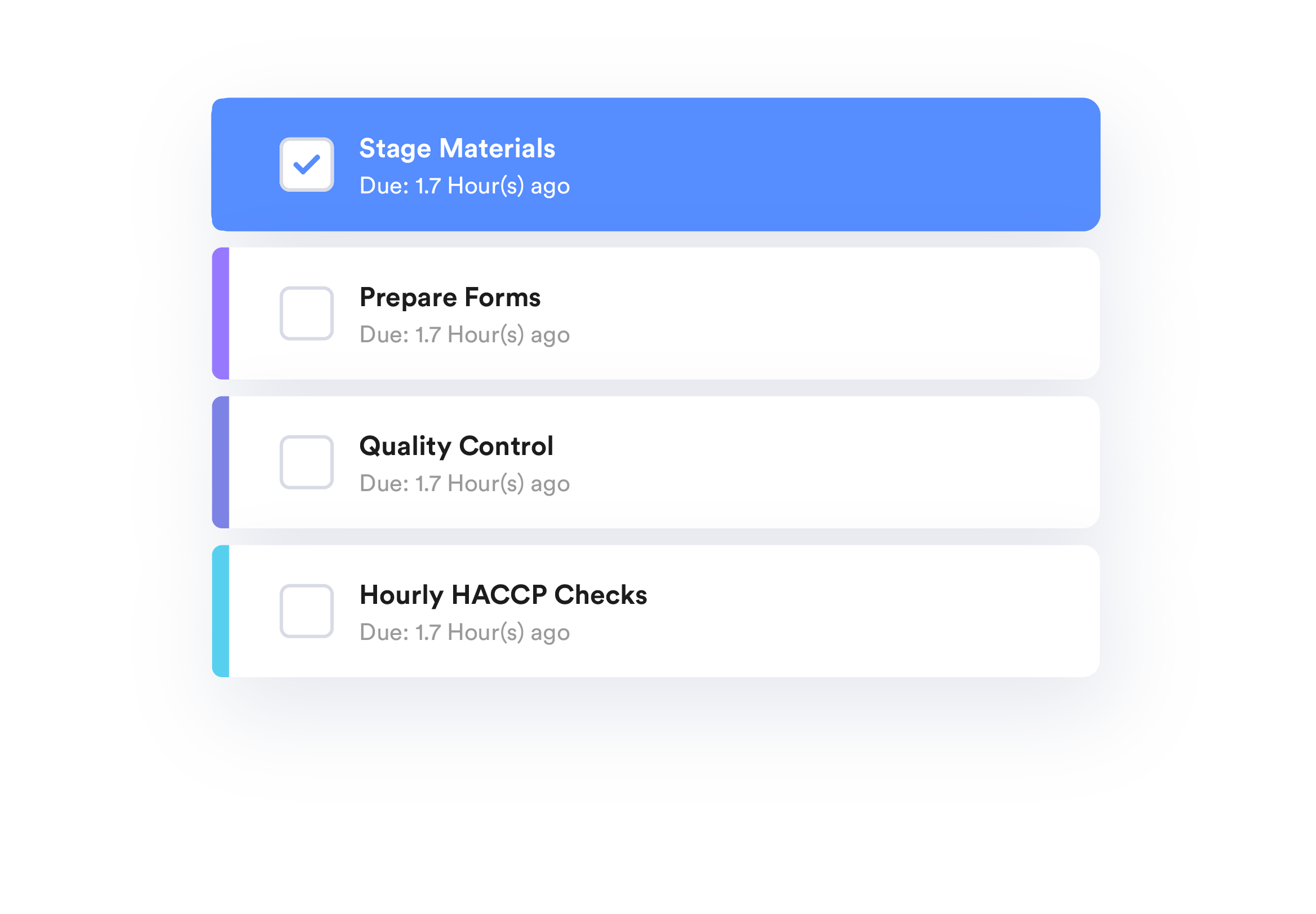
Real-Time Quality Data Collection
TrakSYS allows you to define and manage your quality control plans. Schedule unique tasks as it relates to products, production steps, materials, labor, and assets involved. Useful for Pre-operational, HACCP, and In-Process inspections. Provide instant access through reports and displays for quicker decision-making. With real-time alerts, notifications, escalations, and the ability to configure automated workflows, TrakSYS gives you the quality management tools to communicate and resolve problems quickly and effectively.
Document and Revision Control
Store documents in the built-in Document Library or link to externally stored files. Provide users quick access to standardize procedures in useful formats – pictures, videos, flowcharts, and checklists – reinforcing Best Practices. TrakSYS Audit feature offers a configurable way to track documents and system revisions. Manage employee training, skill sets, certifications, authorization, and security clearance.
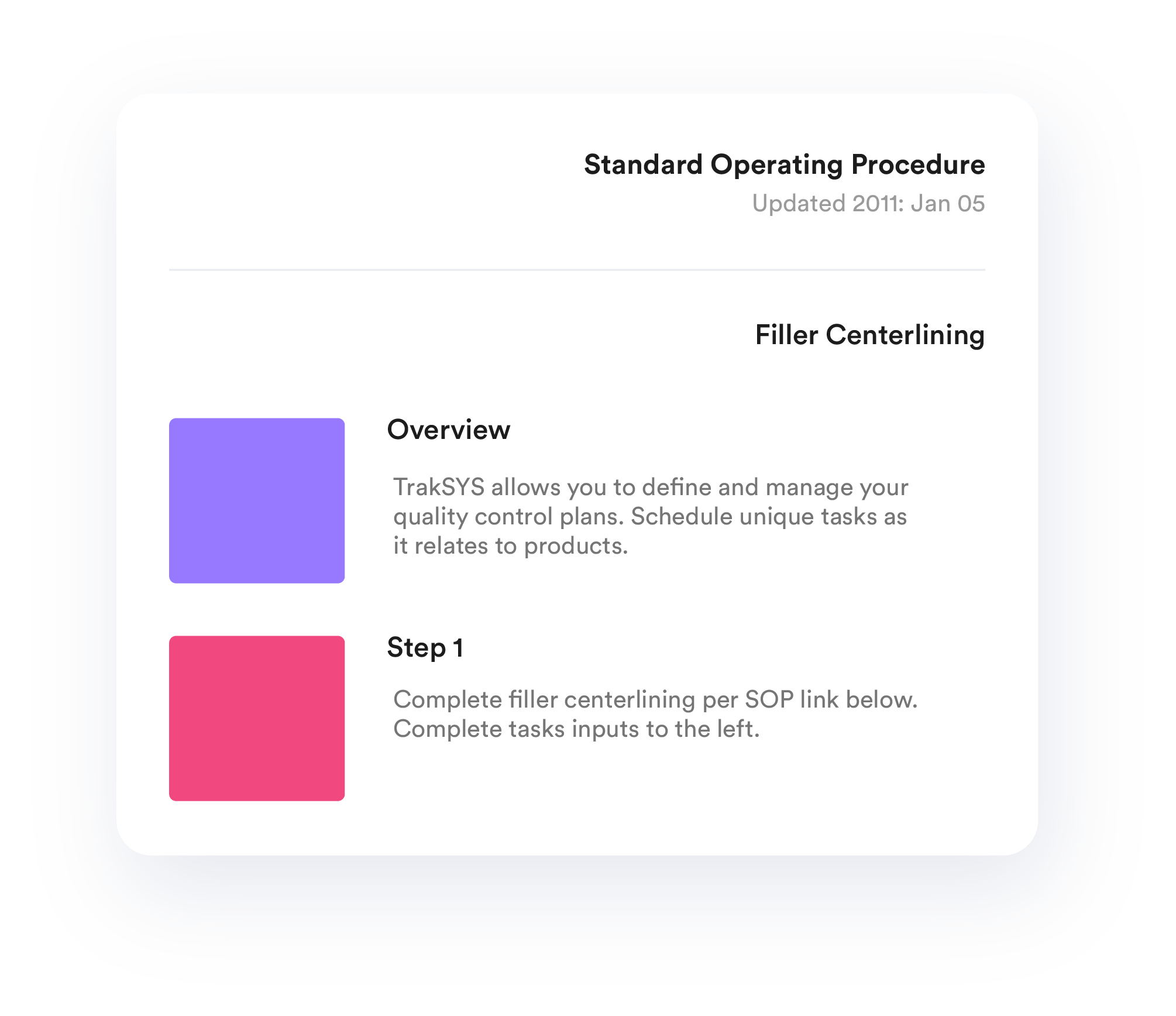
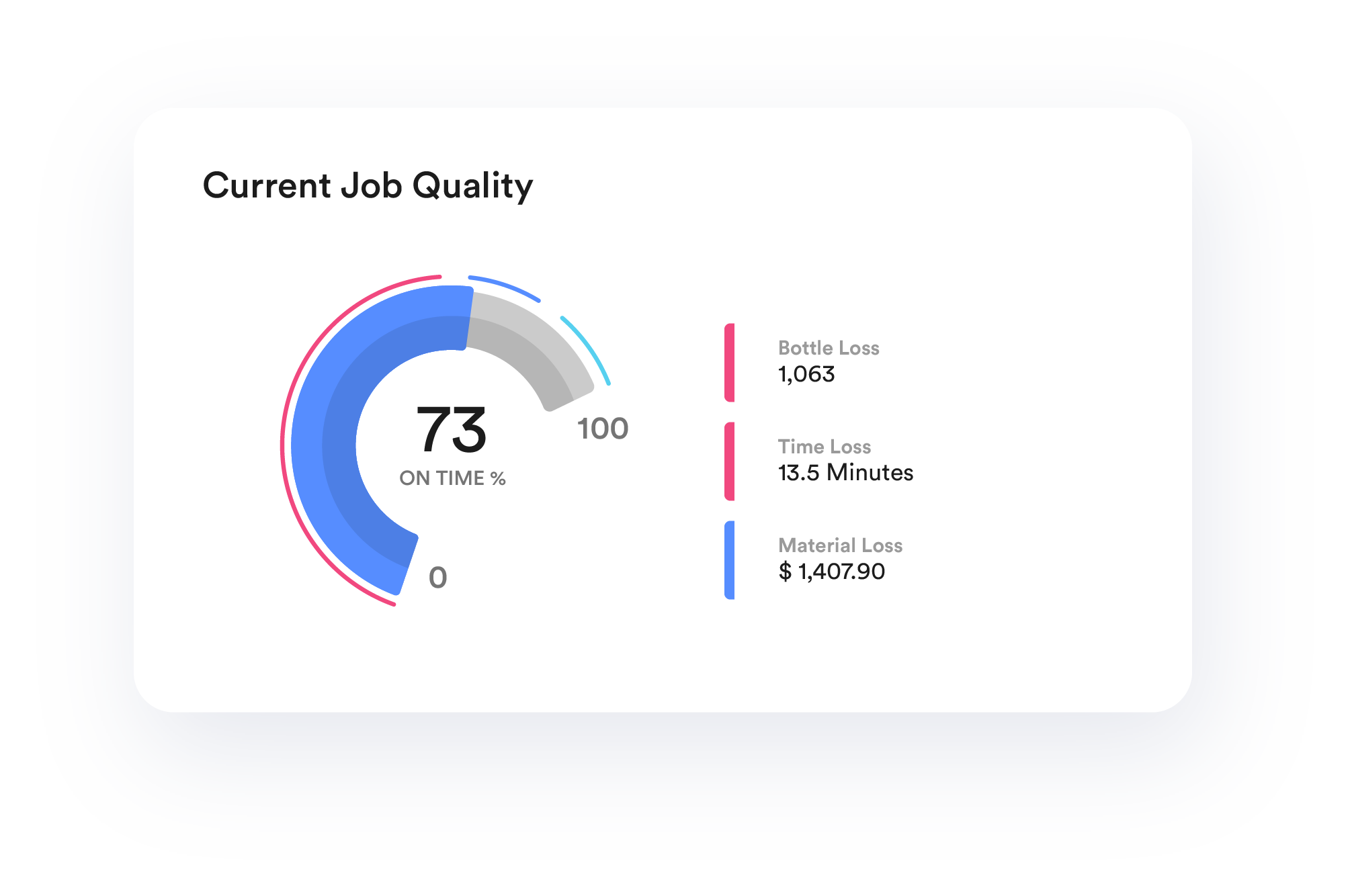
Track and Manage Scrap and Product Defects
Connected to your existing automation infrastructure, TrakSYS provides a clear view of what is happening on your plant floor and informs you of events requiring attention. Engage operators to detail specific root causes or corrective actions, to leverage their knowledge, for quality improvement.
Real-Time SPC
Display product or process measurements with statistical process control (SPC) to regulate quality during the manufacturing process. Data can be gathered through manual input or seamlessly connect to in-line or offline measurement equipment. With real-time alerts and notifications, adjustments can be quickly made to improve process capabilities and minimize the costs of poor quality or product give-away.
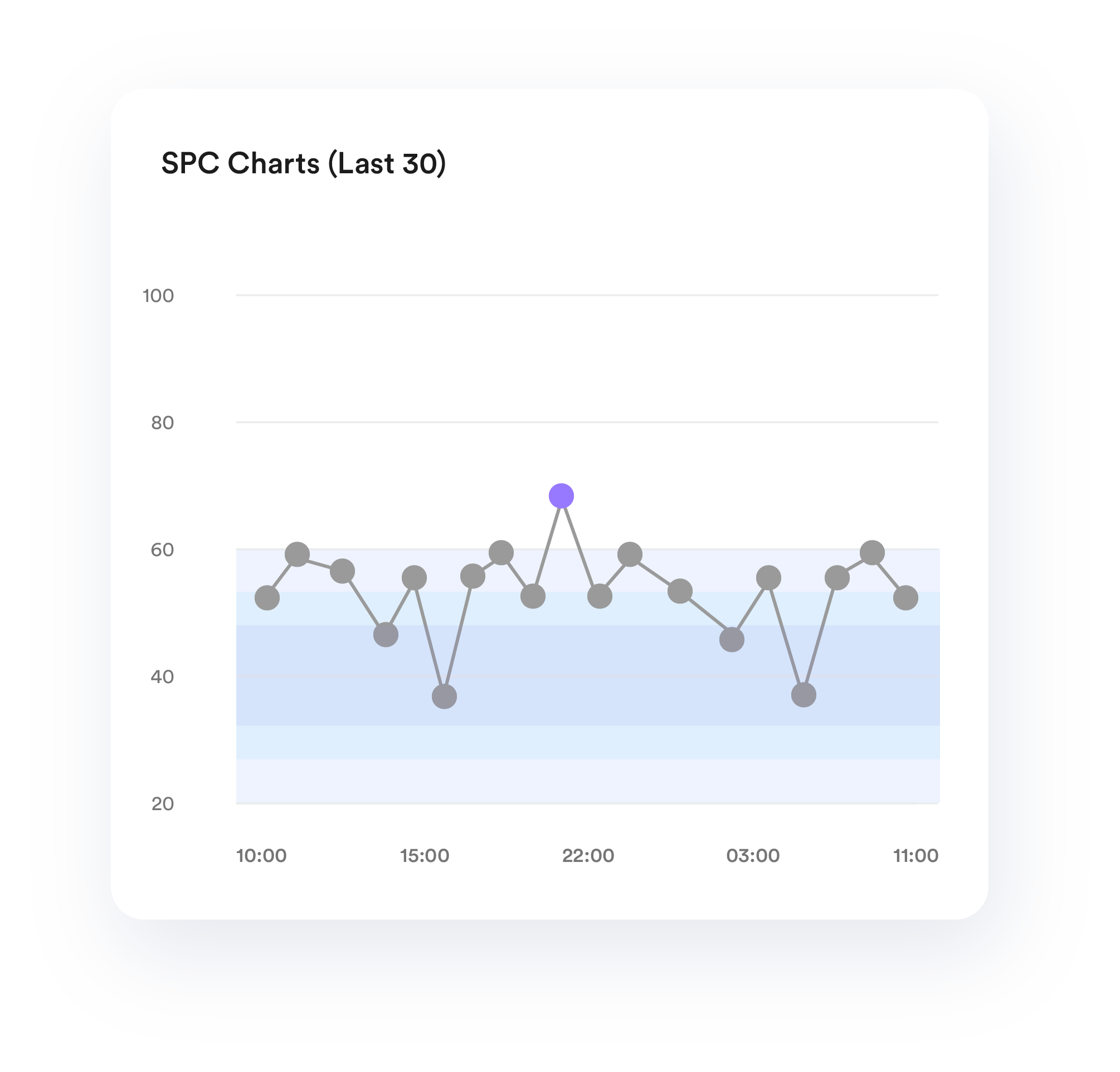
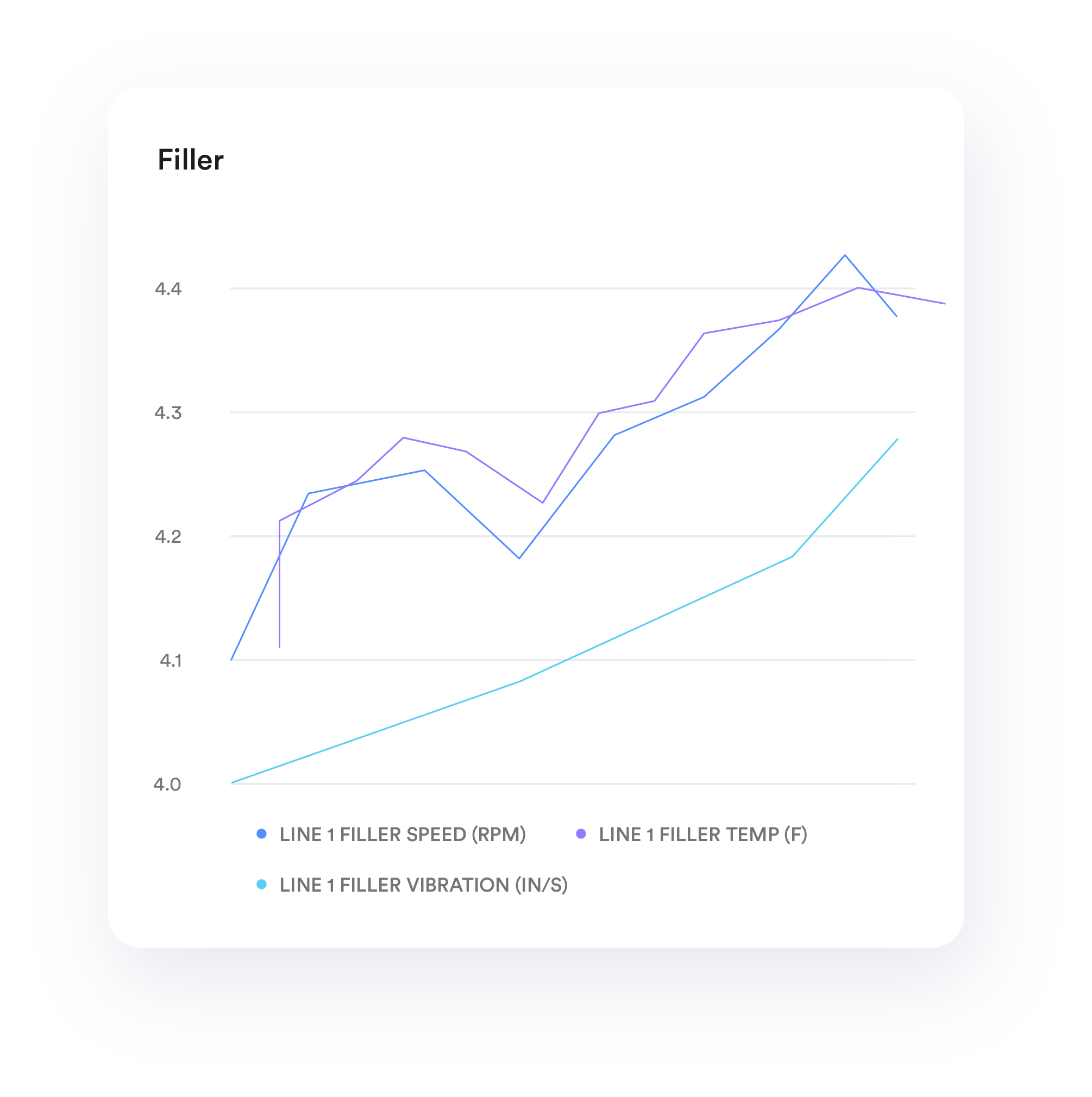
Data Historian
Connect to automation to record and retrieve time-series production and process data. Data Historian further enhances Traceability, enabling users to analyze sources of variation, identify process improvement opportunities, and quickly troubleshoot root causes.
Customer Complaint Management
Record, track and analyze customer complaint trends. Use TrakSYS Traceability to identify if complaints are originating from specific production dates, shifts, products, batch numbers, lot numbers, and production lines. Identify root causes, monitor eliminated reoccurring issues, and determine if corrective and preventive actions are effective.
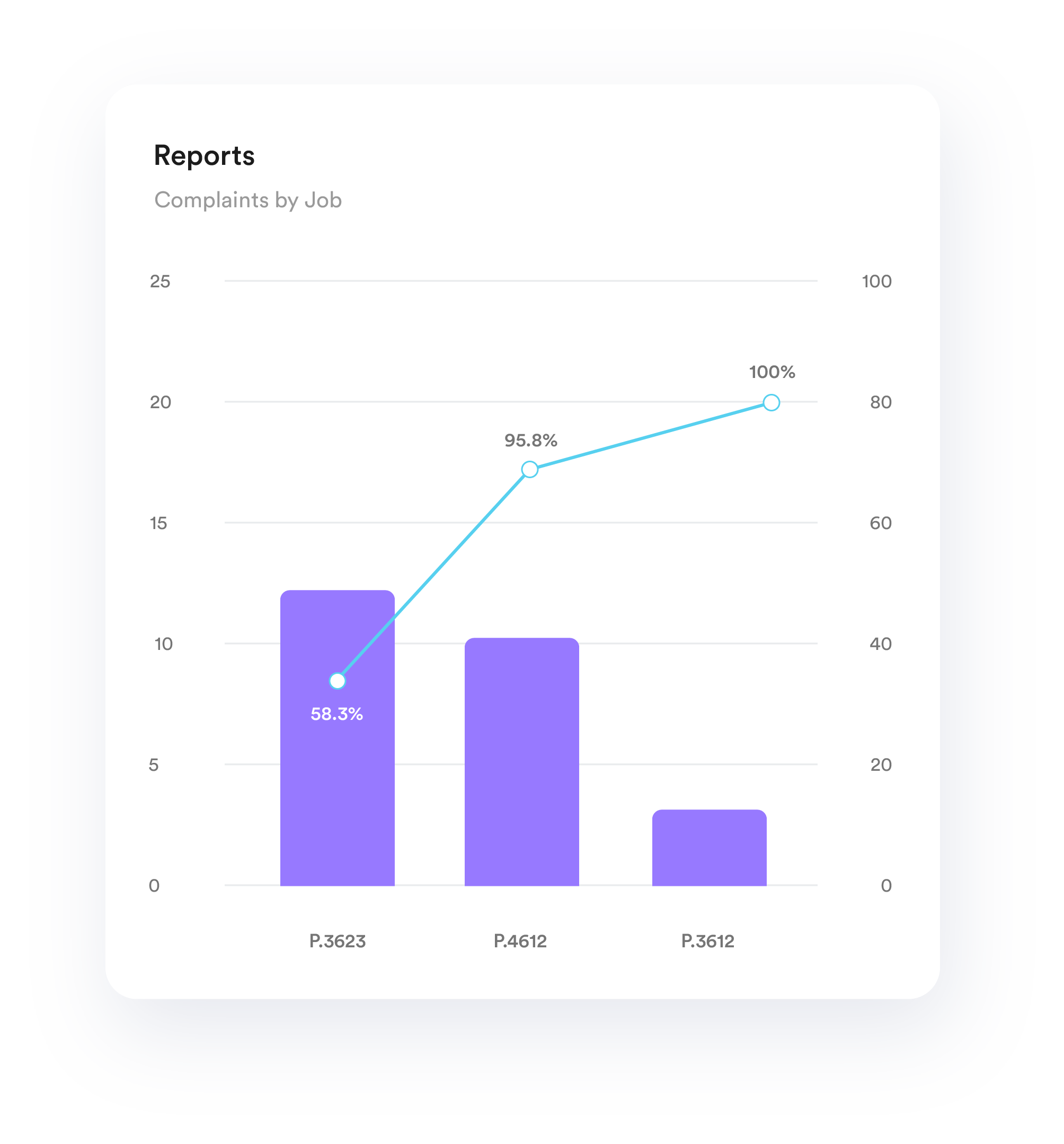
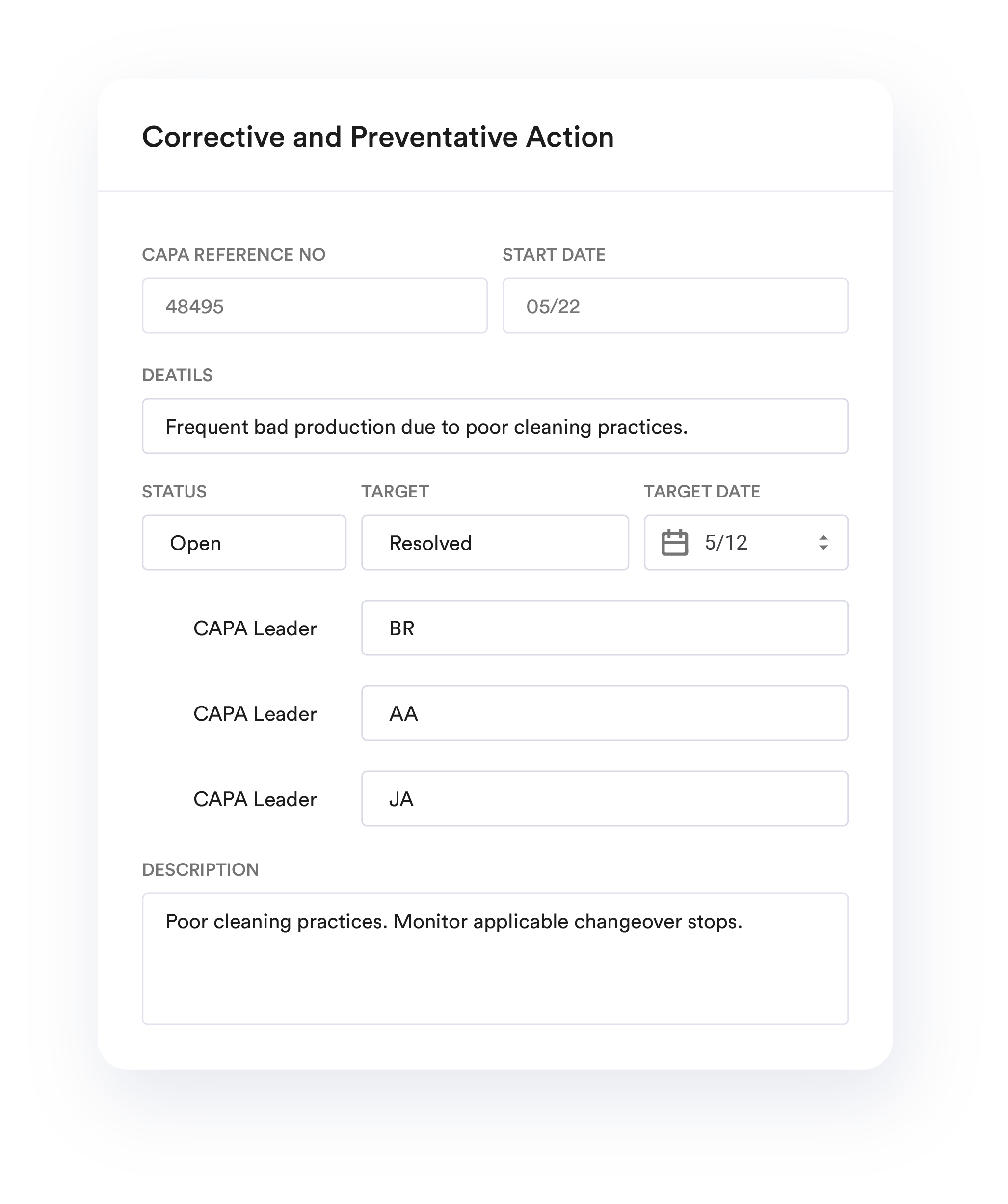
Non-Conformance/Corrective and Preventive Action Management
Record, track, and document non-conformances through to resolution. Drive greater supplier performance, improve customer satisfaction, and speed up the resolution of non-conformances.
Ensure compliance and elevate product quality across the line.
Quality Management Metrics & Reporting
Gain visibility into production operations, including status of QC tasks, failed tasks, SPC violations, process performance, and product quality trends. Quickly determine areas of the factory that require corrective action and prioritize your quality improvement plan.
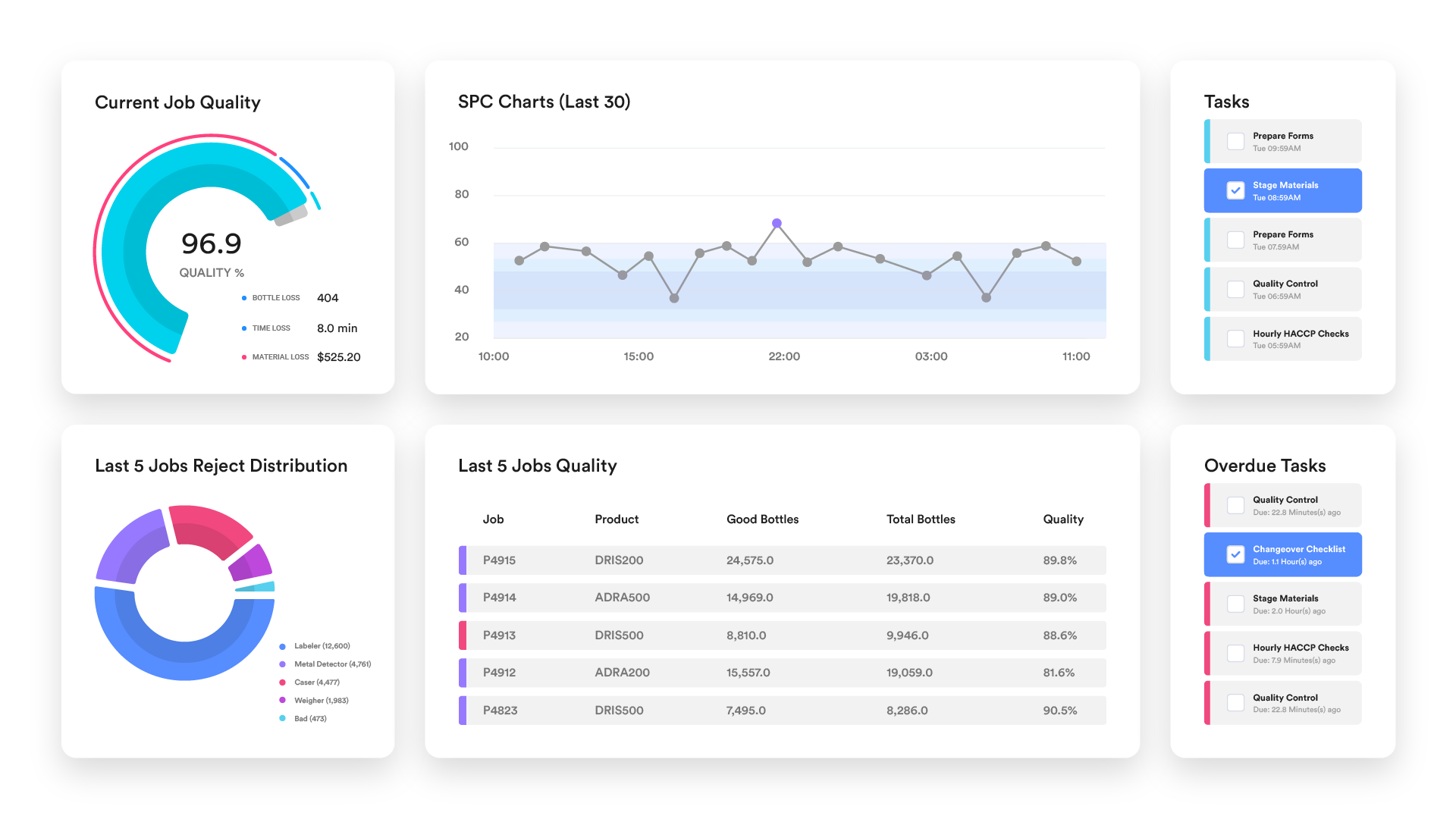
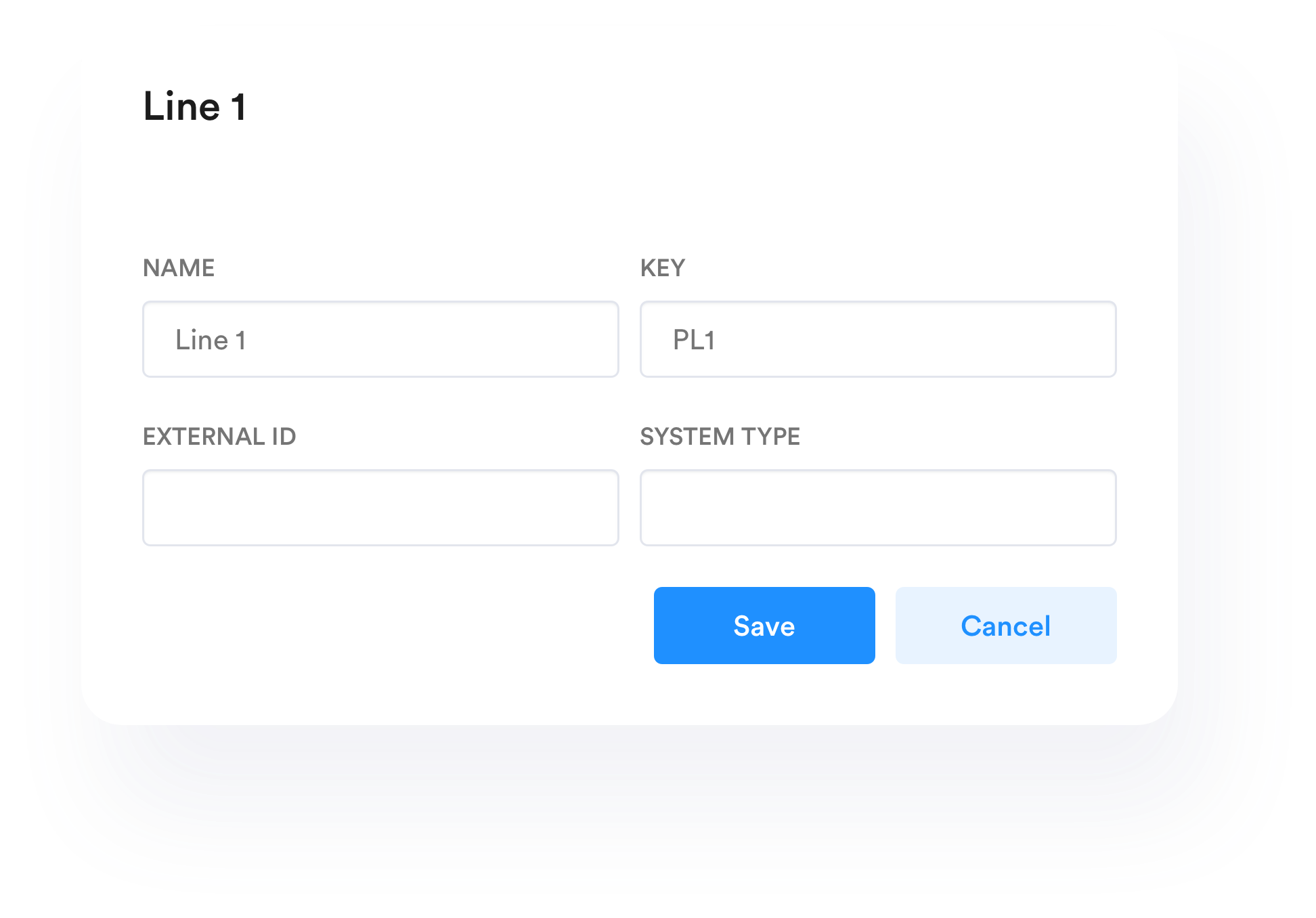
System Configurability
Web-based configuration tools and an integrated scripting environment allow the construction of tailored quality management solutions without the need for custom code.
Extensibility
TrakSYS is a full manufacturing operations management (MOM) platform with standard function libraries that can be readily adjusted to create focused solutions in a fraction of the time compared to traditional solutions development. This important functionality delivers both rapid deployment and cost-effective extensibility.
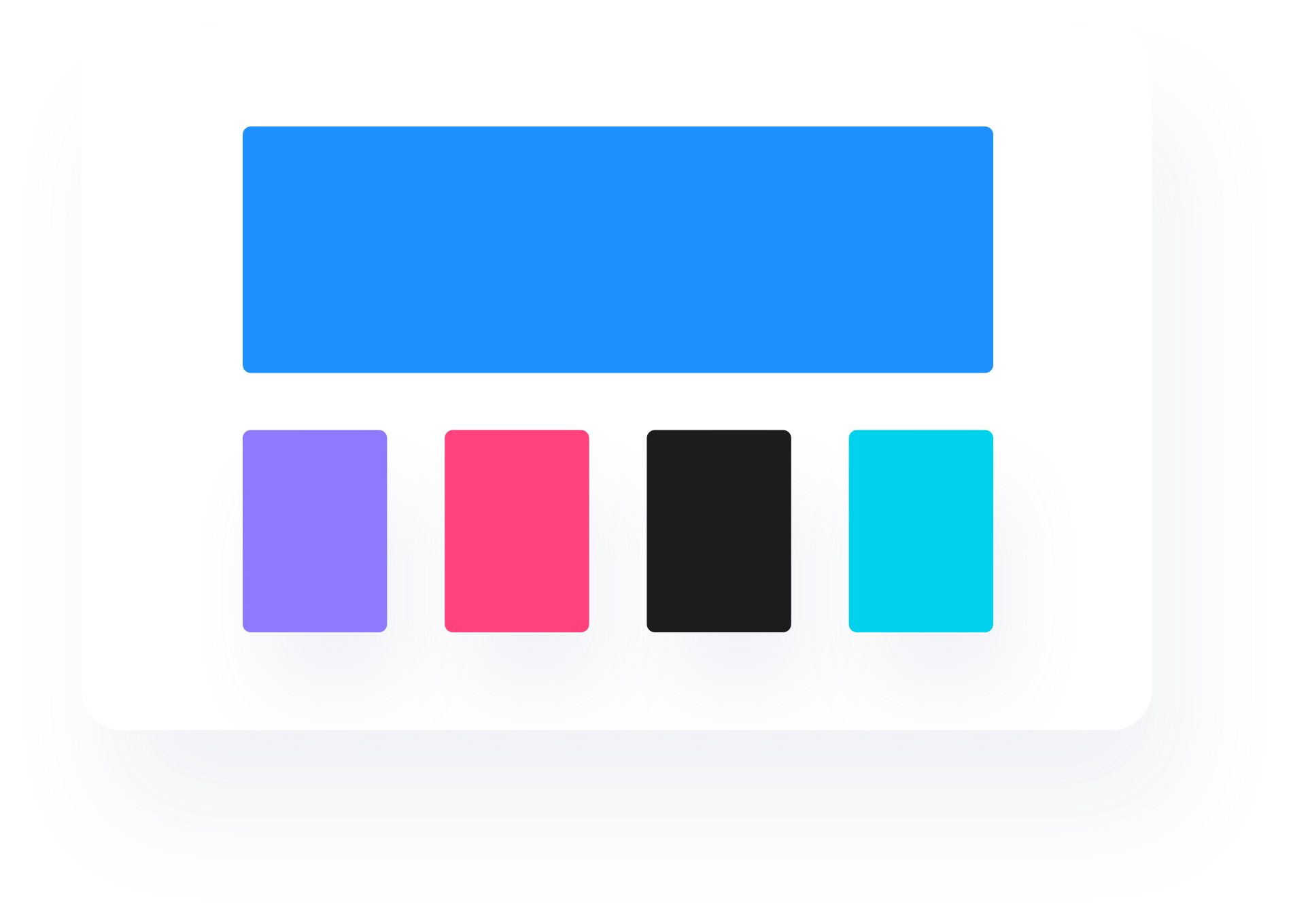
What are You Working on Right Now?
Performance? Quality? E-Records? Tell us what you’re working on.
Chances are, we can help.