In today’s rapidly evolving and expanding marketplaces, the success and viability of a manufacturing operation can be safely summed up thusly: uptime equals profitability, downtime equals profit loss. While that analysis may seem superficial, there is no denying that, in the pursuit of meeting product demand, capturing market share, and bolstering their bottom lines, manufacturers need to be making the most out of every minute of production.
That said, there are several factors that hinder the overall productivity of an operation, including outdated machinery, misaligned management practices, supply chain inefficiencies, and failure to update business-critical software and processes. Being able to identify and quantify these competing factors allows production leadership to solve problems, eliminate waste, and create more efficient, profitable operations. While far from a cure-all, Overall Equipment Effectiveness (OEE) is a tried-and-true key performance indicator (KPI) that, when properly calculated and capitalized on, can elevate production, unlock capacity, and set manufacturers on the path toward operating as efficiently and effectively as possible.
Table of Contents
What is OEE in Manufacturing?
Simply put, OEE measures the overall effectiveness of a piece of manufacturing equipment on a scale of 1-100, with 100 representing total production utilization with zero downtime.
The OEE framework was developed in the late 1980s by Seiichi Nakajima in combination with another Nakajima concept called Total Productive Maintenance (TPM). The original goal of OEE was to improve product quality and total uptime by eliminating as many maintenance and production issues as possible. Today, OEE can be used as a baseline to track progress over time, as well as a benchmark to compare the performance of a specific production asset to other in-house assets or industry standards.
While the foundation of OEE has remained the same throughout the years, the technology manufacturers use to measure and improve their performance has evolved.
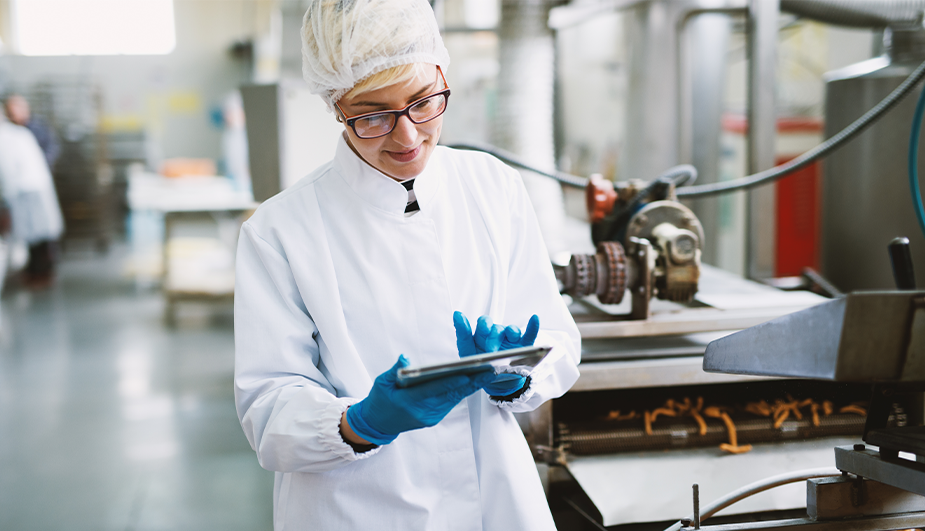
What are the Three Factors that Determine OEE?
OEE is composed of three factors:
-
- Machine Availability: How readily available the machines within the production are.
-
- Machine Performance: How efficiently machines are running within the production.
-
- Production Quality: The condition of the end product.
Machine Availability
To quantify machine availability, divide operating time by planned production time, then multiply by 100.
Availability % = (operating time ÷ planned production time) X 100
Operating time (or run time) refers to the time span during which the machine is actively running and operational. Planned production time is the period during which the machine is scheduled to be available for production. A machine is considered available if it is in working condition and ready to be used.
There are typically two types of availability losses that are considered when calculating OEE:
-
- Planned events: Maintenance, cleaning, upkeep, shift changeovers, etc.
-
- Unplanned events: Machine breakdowns, raw material shortages, operator errors, etc.
Machine Performance
To calculate machine performance, divide ideal cycle time by actual cycle time, then multiply by 100.
Performance % = (ideal cycle time ÷ actual cycle time) X 100
Ideal cycle time is the shortest possible amount of time the equipment needs to produce a finished product. Actual cycle time is the time it takes to produce the product in the real world, taking production inefficiencies into account.
Common causes of performance losses can include:
-
- Minor stops: Machine jams or user errors such as incorrect machine settings and improperly executed standard operating procedures (SOPs).
-
- Sub-optimal speeds: Equipment operating either too slowly or too quickly due to things like inadequate maintenance, asset overallocation, and user errors such as inefficient machine operation.
It is often the case that stoppages are so brief, they slip beneath the radar of human observation. However, such micro-stoppages compounded over a day or week can result in significant downtime, making it that much harder for manufacturers to achieve their production goals and improve their on-time and in-full order percentages.
Production Quality
To calculate production quality, divide quality units by total units, then multiply by 100.
Production Quality % = (quality units ÷ total units) X 100
Quality units refer to the number of units that align with pre-defined quality standards. Total units, on the other hand, include all finished goods, whether they met or fell short of the ascribed quality standard. Defective units (those which did not meet the quality threshold) can be broken into two groups: those that must be reworked to adhere to quality standards and those that must be scrapped as they are beyond the point of repair.
When it comes to lapses in quality, the culprits can be varied and may require a multi-pronged approach to resolution. Having access to historical trends helps enable and enforce statistical process control (SPC)—a vital metric for ensuring consistent quality. Outside of SPC, being able to conduct thorough root cause analysis can shed light on the drivers of specific quality losses, which run the gamut from things like equipment in need of upkeep to team members in need of additional training and the quality of individual raw materials.
How to Calculate OEE
Now that we have broken down the three aspects of production that inform Overall Equipment Effectiveness, it is time to discuss how to accurately calculate this KPI. To determine OEE, multiply availability by performance and quality.
OEE = (availability) X (performance) X (quality)
While an OEE score of 100% represents perfect production, industry-wide OEE benchmarks dictate that manufacturers should realistically aim for a score of approximately 85%, which represents world-class production. Many manufacturers’ scores sit around 60%, which is fairly typical but indicates room for improvement.
OEE scores provide valuable insights into the effectiveness of manufacturing processes, but they fail to dig deeper into the root causes of productivity—and profit—losses. Manufacturers must look deeper into individual availability, performance, and quality calculations to fully understand the origins of these losses. They can do this by engaging with technologies purpose-built to optimize manufacturing processes.
Leveraging an MES to Calculate OEE
Though there are plenty of OEE point solutions on the market, it’s not uncommon to find manufacturers who report world-class OEE scores while missing production deadlines or maintaining sub-optimal fill rates. The discrepancy between OEE scores and actual efficiency likely points to inaccurate OEE calculations and/or a need to strengthen production technology. Many common production inefficiencies could be addressed by working with a comprehensive manufacturing execution system (MES).
Utilizing an MES to capture OEE on its own or work in conjunction with an existing OEE solution can help shed light on hindering factors across various manufacturing processes. It can also strengthen other areas of production that inform a facility’s overall OEE metric.
An MES like TrakSYS™ provides concurrent, real-time calculations of availability, performance, and quality to improve production OEE. Having access to real-time data and performance insights lets manufacturers not only monitor but understand OEE performance. These metrics enable teams to perform root-cause analyses to identify why performance is dropping and implement proactive improvements.
With a best-in-class MES platform, manufacturers can solve production problems, eliminate waste, and reach peak OEE. That means more efficient, profitable, and predictable operations.
To learn more about improving the accuracy of your OEE metric and accelerating productivity, contact us today.