With their ability to create dynamic, real-time digital replicas of physical assets, processes, and systems, digital twins have become a focal point in modern manufacturing. Enhancing operational visibility and bolstering connected manufacturing, the conversations around digital twins span from the shop floor to executive boardrooms. Whether you are working on your own digital twin initiative or are just looking to learn more about the topic, this blog provides an overview of how TrakSYS™ facilitates the creation—and optimal utilization—of this powerful technology.
Table of Contents
Real-time Data Integration
The foundation of any effective digital twin is real-time data. Through its native interoperability, TrakSYS collects, contextualizes, and correlates real-time data from various sources, including digital systems such as ERP, SCADA, and CMMS, as well as physical assets and IoT devices. This continuous data flow ensures that the digital twin remains an accurate and current reflection of physical operations, enabling precise monitoring and control.
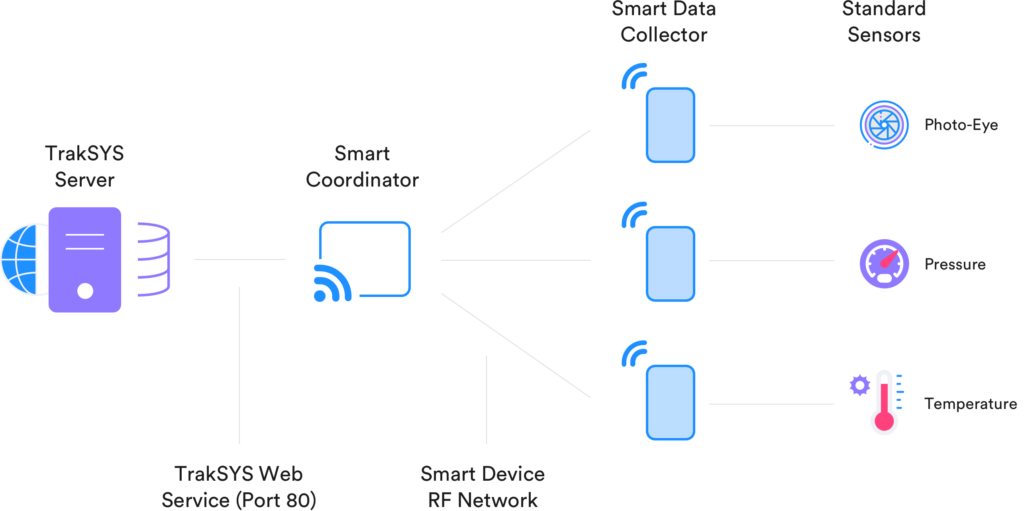
Simulation and Analysis
A critical advantage of digital twins is their ability to simulate and analyze various scenarios. The “what-if” analysis options in TrakSYS Algorithmic Production Scheduling allow for simulating future resource load and consumption scenarios, enabling manufacturers to test different operational strategies virtually. With that functionality, businesses can more accurately determine the impacts of potential changes and use that information to devise data-driven, risk-averse strategies.
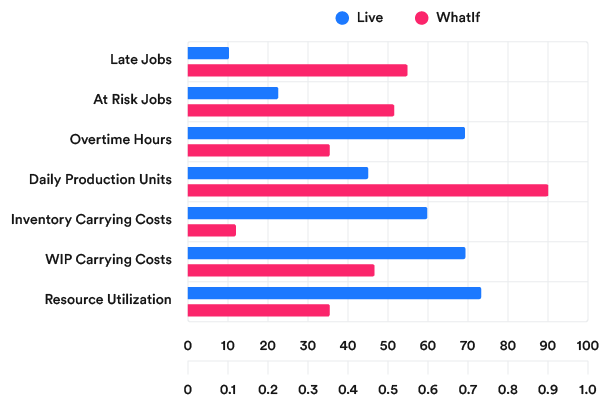
Visualization
Process twins (a type of digital twin) are the digital representation and execution of a previously manual process. Utilizing TrakSYS Visual Workflow, users can recreate complex processes in a simple drag-and-drop web interface. Being able to ‘see’ the workflows executing throughout the process steps in real-time enables everyone—from the shop floor to the board room—to observe the real-time state of a process or workflow and be instantly made aware should any deviation or bottlenecking occur.
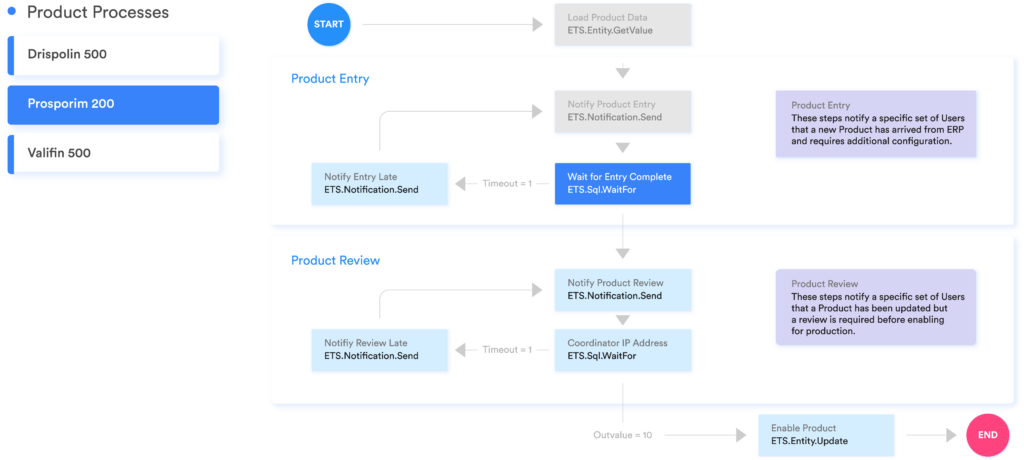
Continuous Improvement
Digital twins offer unparalleled opportunities for process optimization and continuous improvement. By continually monitoring performance metrics and applying advanced analytics, manufacturers can refine their processes to minimize waste and maximize efficiency. The feedback loop facilitated by digital twins is essential for driving sustained improvements and adaptability in a rapidly changing manufacturing landscape.
Conclusion
Digital twins represent a transformative advancement in manufacturing, offering unparalleled insights and control over operations. By utilizing TrakSYS to unify real-time data collection, unlock advanced simulation capabilities, and leverage comprehensive modeling, manufacturers can experience greater efficiency, predict and mitigate issues, and foster continuous improvement. To further explore how TrakSYS and digital twins can elevate your manufacturing operations, contact us today.
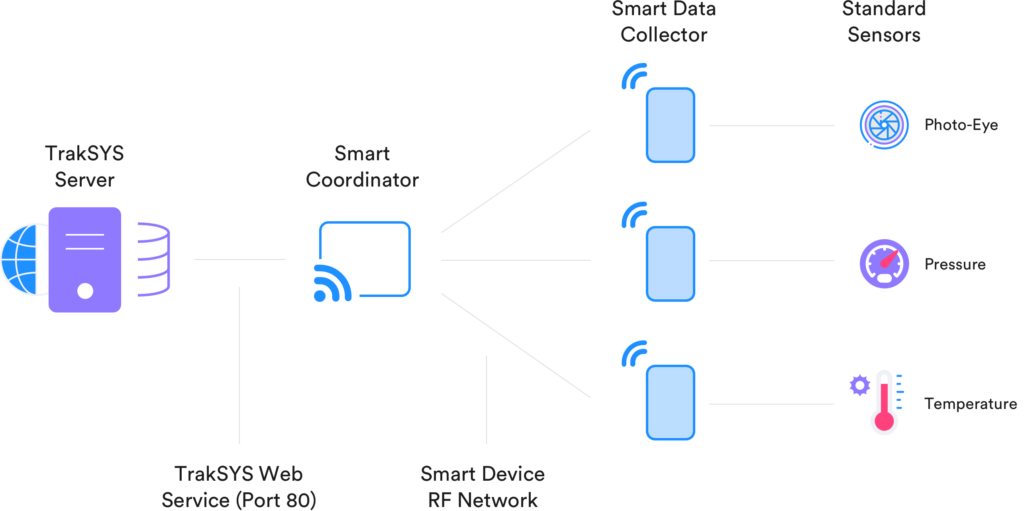
FAQs
A digital twin is a dynamic, real-time digital replica of physical assets, processes, and systems. It allows manufacturers to monitor, analyze, and optimize operations through a virtual model that reflects real-world conditions.
TrakSYS facilitates the creation of digital twins by integrating real-time data from various sources, providing visualization and monitoring tools, enabling simulation and analysis, and supporting detailed process modeling environments.
TrakSYS collects, contextualizes, and correlates real-time data from various sources, including digital systems such as ERP, SCADA, and CMMS, as well as physical assets and IoT devices (like the TrakSYS Smart Devices).
TrakSYS enables users to reconstruct their process workflows via a visual, logic-based workflow engine and create various 3D environments.
Yes, TrakSYS includes advanced simulation and predictive analytics capabilities. It allows users to simulate scenarios, predict potential issues, and conduct what-if analyses to understand the impact of changes on production processes.