Table of Contents
Short Staffed?
Let’s dive right in. Manufacturers worldwide are striving to restore their workforces to pre-pandemic levels of strength and productivity. Despite these efforts, labor and staffing challenges persist. In the United States, the manufacturing sector has recovered a portion of the 1.4 million jobs lost during the pandemic, yet over 600,000 positions remain unfilled. Similarly, European manufacturers have faced industrial and economic turbulence, leading to a reduction of more than 800,000 manufacturing jobs since 2019.
To delve deeper into these issues, Parsec conducted its 2024 State of Manufacturing Survey, engaging over 1,000 industry leaders across North America and Europe. The survey revealed a range of challenges—from supply chain disruptions to reshoring initiatives and increasing digitization—but a common thread emerged: every respondent faced at least one workforce-related obstacle. This blog explores the most prevalent labor challenges identified and examines strategies that can help manufacturers overcome them.
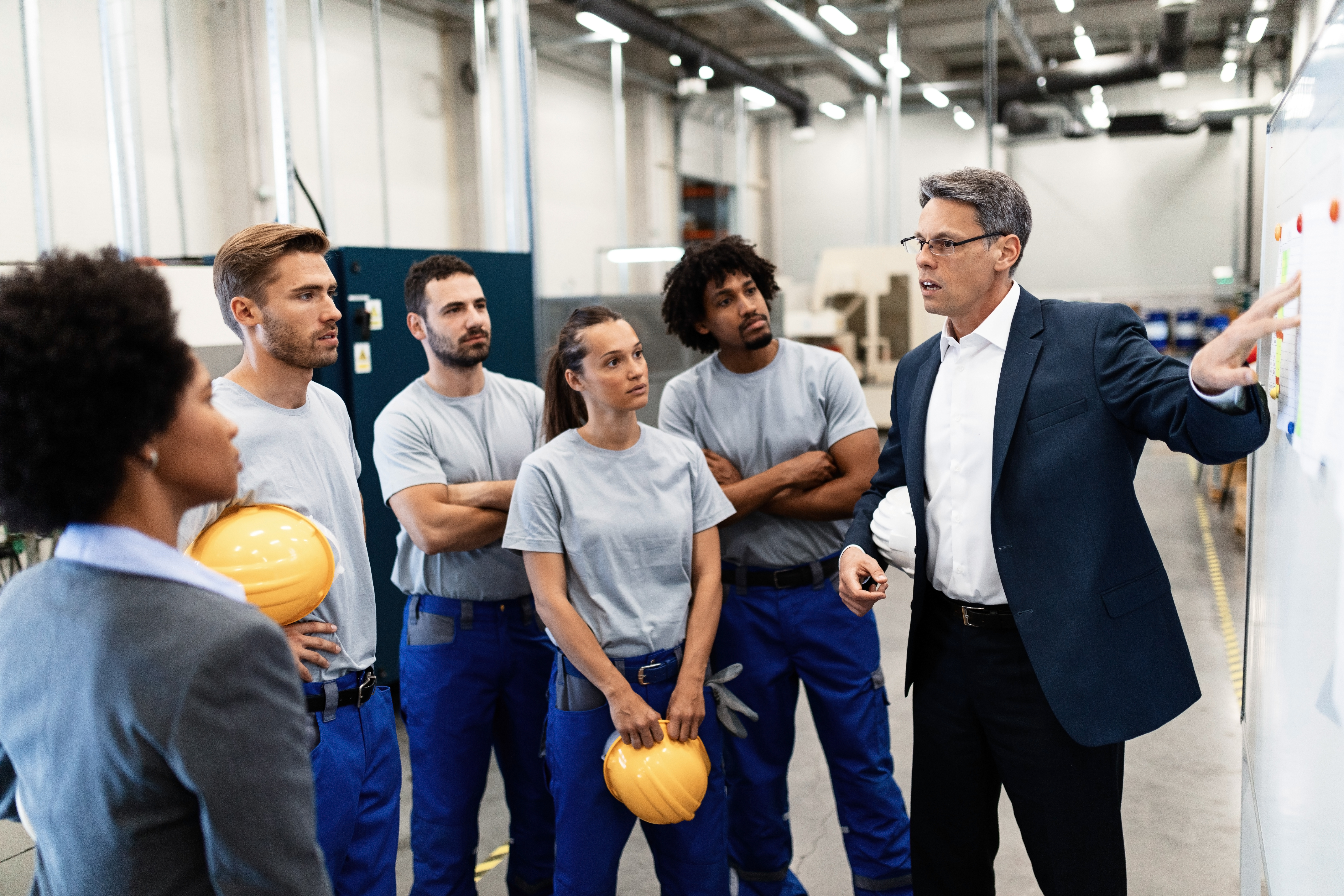
Finding and Retaining Qualified Candidates
A significant hurdle for manufacturers is sourcing and retaining qualified talent. According to the survey, 43% of North American and 40% of European manufacturers struggle to find suitable candidates. Several factors contribute to this challenge:
- Wage Competition: Over one-third of manufacturers report difficulties in attracting and retaining skilled workers due to competitive wages (North America: 36%; Europe: 41%). This wage pressure also impacts retention, with 37% of European and 33% of North American manufacturers citing it as a concern.
- Workforce Demographics: An aging workforce adds another layer of complexity, as core workers retire faster than they can be replaced. This demographic shift affects 32% of European and 37% of North American manufacturers.
These staffing challenges not only impede production but also hinder manufacturers’ ability to adapt to market demands. Whereas younger team members may be more adaptable to technologies a company seeks to incorporate, they may lack the hands-on experience of their forbearers.
Maintaining a Technologically Skilled Workforce
Speaking of technology adoption—as manufacturing processes become more digitized, the need for a technologically adept workforce grows. However, more than one-third of manufacturers (North America: 37%; Europe: 42%) find it challenging to maintain a technically skilled workforce. This skills gap is particularly evident in the adoption of artificial intelligence (AI); approximately 34% of European and 30% of North American manufacturers feel that a lack of skilled talent inhibits their ability to implement AI technologies.
With 99% of North American and 98% of European respondents exploring AI use cases, upskilling the workforce is imperative. Industry 4.0 isn’t just about adopting new technologies; it’s about integrating them effectively with human expertise.
Implementing New Technologies to Address Challenges
To tackle labor challenges, manufacturers are increasingly turning to digitalization and automation. The survey highlights several outcomes companies are looking to achieve through their various toolsets:
- Reducing Waste: 45% of North American and 36% of European manufacturers see implementing new technologies as a cost-saving measure. Reducing waste not only improves the bottom line but also frees up resources that can be allocated to employee compensation.
- Improving Efficiency: Half of European (50%) and 47% of North American manufacturers believe that new technologies will enhance operational efficiency, creating a more optimized working environment for skilled employees.
- Enabling Data-Driven Decision-Making: Over 44% of North American and 43% of European manufacturers hope that new technologies will strengthen their ability to make informed, data-driven decisions. This capability allows for better demand forecasting, reduced equipment errors, and improved safety measures.
- Future-Proofing Operations: Digitalization enables the integration of cutting-edge technologies like AI and the Industrial Internet of Things (IIoT), making facilities and workers more advanced, efficient, and competitive.
That said, the adoption of any technology ultimately hinges on its effective and consistent utilization by a workforce. Unfortunately, proper onboarding and training continue to be a challenge for 38% of manufacturers across both regions.
The Road Ahead
Manufacturers are making strides to overcome the labor downturn of recent years, but challenges remain. To address labor issues and work toward a revitalized workforce, business leaders can benefit from:
- Investing in Workforce Development: Upskilling initiatives and targeted training programs are critical to bridging the skills gap. Manufacturers must prioritize ongoing education in emerging technologies, ensuring that employees can adapt to an evolving industry landscape.
- Enhancing Recruitment and Retention Strategies: Competitive wages, robust benefits packages, and flexible work environments can help attract and retain talent. Additionally, fostering a strong company culture and providing clear career advancement opportunities can improve employee satisfaction and longevity.
- Pursuing Digital Transformation: While automation and AI offer powerful solutions to labor shortages, their success depends on proper implementation and workforce integration. Companies must invest in operationally unifying technology and provide comprehensive training to ensure team members understand the solutions’ value and their role in making that value possible.
- Leveraging Data for Smarter Workforce Planning: By utilizing real-time analytics and predictive workforce modeling, manufacturers can proactively address staffing shortages, optimize workflows, and anticipate future labor needs more effectively.
The manufacturing sector is at a pivotal moment, where workforce resilience and technological innovation must go hand in hand. By embracing strategic investments in talent and technology, companies can position themselves for long-term success, ensuring a more agile, efficient, and future-proof industry.
To learn more about the current state of manufacturing, download our European and North American 2024 State of Manufacturing Reports today.