Today’s manufacturers often operate across many sites, regions, countries, and even continents. Ensuring consistent performance, quality, and visibility across these locations can present major challenges, yet is critical for enterprise success.
Single Instance Multi-Site (SIMS), enables businesses to install a single instance of TrakSYS and access it across multiple locations to create a unified and standardized operational model. With a SIMS deployment, manufacturers can use TrakSYS to remotely connect as many—one customer has connected over 50 of their sites—or as few of their facilities as they want, no matter where in the world they’re located.
In this blog we take a look at what SIMS is, how it works, and discuss the circumstances that make it an ideal deployment model for manufacturers across industries. Sound interesting? Let’s dive in.
Table of Contents
What is SIMS?
SIMS stands for Single Instance Multi-Site. With this offering, TrakSYS is installed once and remotely connects to multiple manufacturing sites across the organization. All sites connect to a single, central TrakSYS database to access and share data, configurations, user interfaces, and more.
While we will explore this further, it is helpful to note that services—such as data collection and advanced planning and scheduling (APS)—have the option to run independently at each plant, ensuring site-specific responsiveness.
When it comes to hosting the main TrakSYS deployment, businesses have three options:
- On servers in the company’s centralized data center
- A private cloud environment
- On-site servers located at one of the manufacturing facilities
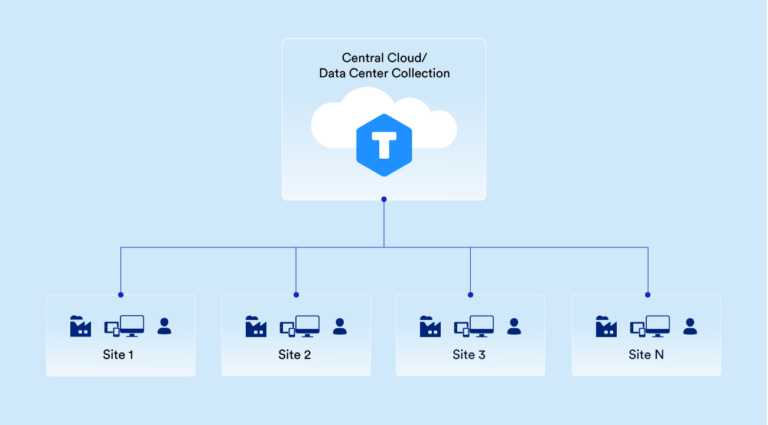
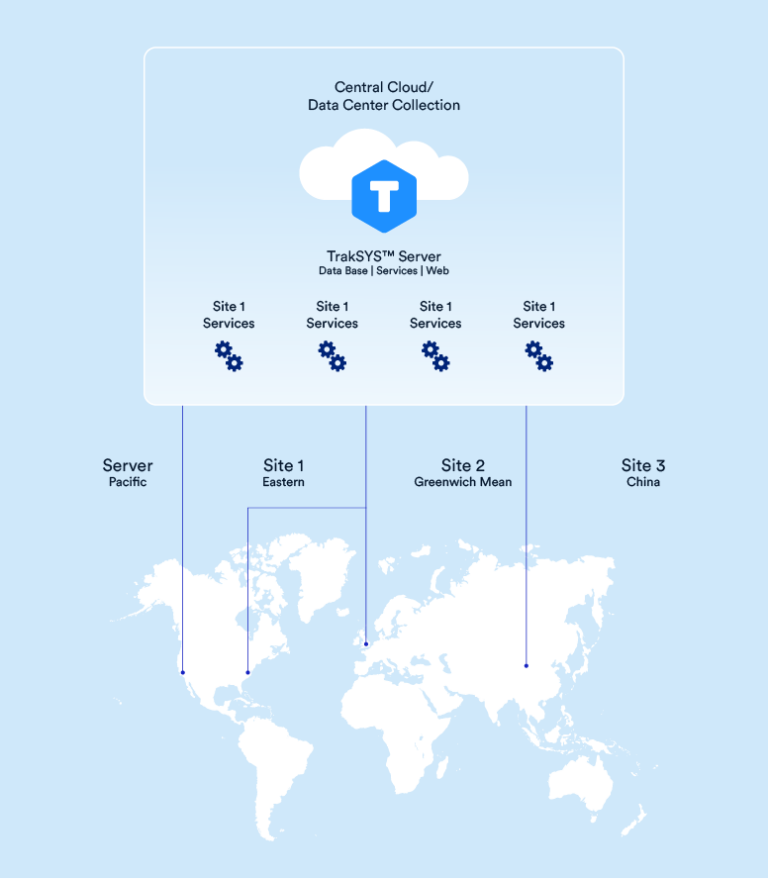
Regardless of deployment method, its important to note that internet connectivity between sites and the centralized TrakSYS web application server is critical to SIMS rollout and success.
Why We Created SIMS
TrakSYS began as an on-premise MES, designed to run on the plant floor where the action happens. Real-time data collection, machine integration, and operator interfaces all demanded proximity to ensure consistent connection.
Now, technology is evolving. Over the past decade, remote network reliability, internet speeds, and cloud infrastructure has improved dramatically. Customers with multiple facilities began asking the Parsec team: “Can we install TrakSYS once and connect all our plants?”
In the early days of developing our SIMS methodology, we worked closely with an array of customers to develop an architecture that complies with the most challenging regional and process differences across sites. Today, SIMS is a proven architecture for manufacturers who want centralized controls and enterprise-wide visibility without compromising plant-level flexibility.
Key Benefits of SIMS
SIMS can provide manufacturers with a more connected, scalable, and efficient way to manage MES across multiple locations. While the technical structure behind SIMS is powerful, it’s the business outcomes that make the approach valuable.
Key benefits include:
Standardization
SIMS has the ability to define and deploy standards across all locations from the central TrakSYS instance. Common workflows, naming conventions, tags, pick lists, and more can all be defined once and rolled out uniformly. This promotes consistency, reduces confusion, and helps enforce best practices across the enterprise.
Central Source of Truth
With one centralized TrakSYS database, organizations gain a single source of truth for all operational data. Metrics, KPIs, system configurations, and processes are consolidated, making enterprise-wide analysis and reporting simpler and more accurate.
Faster Rollout for Additional Sites
The initial TrakSYS installation is comparable to any implementation. But with SIMS, every subsequent site rolls out more quickly and easily, benefiting from shared configurations and infrastructure. For organizations planning to scale their MES footprint, this can mean faster time-to-value and more efficient expansion.
No Need for On-Site Servers
With SIMS, smaller or newer plants that lack the IT resources to host on-premise MES can still participate in the enterprise MES initiative. They connect to TrakSYS remotely and gain full MES capabilities with minimal local overhead.
Timely Updates
SIMS connectivity makes updates quicker and more uniform. Rather than maintaining multiple installations, you can implement changes once in the central instance, and they will flow to all sites automatically.
Opportunity for Cost Savings
SIMS may provide cost efficiencies. Users purchase one central instance of TrakSYS and scale it by adding licenses per site. That said, pure cost savings are not the aim of a sims deployment. As business may need to update servers and/or cloud capabilities to facilitate this model, the true value is derived from the points above.
Key Considerations for SIMS
While SIMS offers valuable benefits, it does require infrastructure maturity to deploy TrakSYS remotely across locations. Since all sites depend on a central server, any downtime at that location can affect all connected plants. Your central environment must be robust, secure, and high-performing. In that vein, in addition to industry standard methods for keeping applications highly-availabe (VM Failover, Database Redundancy, Network Load Balancing), TrakSYS also offers platform-specific Service Failover to keep your mission critical operations running even if hardware or network issues occur.
Organizations seeking to implement SIMS must evaluate:
- Internet connectivity and bandwidth at each site.
- Central server capacity and performance.
- Data volume, number of users, and real-time processing needs.
It is helpful to remember that TrakSYS is a sophisticated platform that performs best with strong infrastructure support. As we noted at the top of this piece, there is the ability to host TrakSYS Services—data collection configuration, APS, etc.—locally, apart from where the main TrakSYS application is hosted. While this can help reduce the load requirement of the host server, it does not intrinsically negate issues around latency, or in any way lead to edge processing or data draw down in the event of a network outage.
Given these consideration, our team is here to help you assess your environment and scale resources where needed to ensure a successful SIMS deployment.
Connected, Yet Customizable
While SIMS enables standardization, it doesn’t demand uniformity. TrakSYS allows each site to operate as autonomously as needed. You can choose how much (or how little) data and configuration to share across plants. Each location can tailor its TrakSYS interface to meet it’s unique needs. Likewise, access to information can be configured based on user permission sets. As an example, a business may determine that Plant Managers should have access to cross-site performance metrics while a site-specific operator can only view/access data pertinent to their site/role.
Beyond that, TrakSYS can support any language and time zones an organization’s employees may need, and automatically organizes tasks and data to be clear and straightforward to each user at each location. This balance between consistency and customization is a key advantage of SIMS. Whether every site runs identically, completely independently, or somewhere in between—TrakSYS can support your operations.
SIMS vs. Multi-Site: What's the Difference?
TrakSYS offers two key deployment models for users looking to implement their MES across multiple locations: SIMS and Multi-Site.
- SIMS (Single-Instance Multi-Site): as discussed, SIMS is a centralized TrakSYS deployment that uses a remote internet connection to run across all locations.
- Multi-Site: by contrast, Multi-Site means installing and maintaining a separate instance of TrakSYS at each location. Each plant runs its own database and system, though standardization can still be achieved through templates and governance. Of note, our forthcoming TrakSYS Cloud offering will help with Multi-Site Management (licenses, versions, and moving templated features from site to site).
Choosing the right model depends on infrastructure, IT strategy, and operational needs. TrakSYS is uniquely flexible—manufacturers can opt for SIMS, traditional multi-site, or even a hybrid of the two.
Conclusion
SIMS can be a powerful option for manufacturers seeking centralized control, streamlined rollout, and enterprise-wide visibility. Whether you’re managing a global network of facilities or simply looking to connect a couple plants, SIMS can help unify your operations and drive efficiencies at scale.
Interested in how SIMS could work for your organization? Contact us to learn more or schedule a TrakSYS demo.
FAQ
What is the difference between SIMS and traditional multi-site MES deployments?
How do I know if my organization is ready for a SIMS deployment?
Can each site still maintain autonomy in a SIMS environment?
What happens if the central server goes down?
Because SIMS depends on a centralized TrakSYS server, a failure at the central location will affect all connected sites. That’s why it’s essential to ensure the hosting infrastructure is robust and appropriately scaled. Many customers mitigate this risk by using private clouds with high availability and disaster recovery configurations. Additionally, There are four levels of safeguarding Parsec supports:
- Hardware redundancy (mentioned above)
- Database redundancy: leveraging SQL Server Always-On Availability Groups
- Web redundancy: leveraging Network Load Balancing
- TrakSYS Service Redundancy: TrakSYS Service failover
It is important to note that, of these, only #4 is a licensed feature. Measures one-three are advisable ways users can help prevent failure and are already fairly standard in the IT space.