Supply-chain disruptions cost the average organization 45 percent of one year’s profits over the course of a decade.1
Our global economy is powered by networks of millions2 of businesses that transform raw materials into delivered goods and services. The significance of these networks or supply chains goes largely unnoticed by the average consumer unless they experience a disruption in the availability, quality, or cost of a good or service they rely upon. When this occurs, however, it signals a much larger issue than an unsatisfactory shopping experience. Disruptions may be caused by a number of factors occurring inside or outside the supply chain. Catastrophic events3 such as the COVID-19 pandemic, China’s subsequent lockdown, the Russian-Ukraine war, and weather-related disasters have exacerbated issues in materials availability, production, and the transportation of goods and services worldwide. Such upheavals can last a month or longer and, on average, are hitting supply chains every 3.7 years4. As they continue to reverberate through our global economy, an abundance of waste is left in their wake.Table of Contents
- Analyzing the Impact of Waste on Supply Chains
- The Cost of Waste
- The Case for Lean Manufacturing
- The Evolution of Lean
- How Lean and Sustainable Principles Work in Tandem for Supply Chain Management
- TrakSYS for Lean Supply Chain Management
- FAQs
Analyzing the Impact of Waste on Supply Chains
Waste5 can come in many forms—excess inventory, machine downtime, and employee productivity to name a few—all of which impact a company’s operations, output, and value to their customers. Inventory can be a double-edged sword when it comes to supply chain agility. While a lack of excess inventory may dull the impact of a sudden drop in demand, it may also bear a negative impact were demand to suddenly surge. The challenge6 for companies is to make their supply chains more resilient without diluting their competitiveness. Understandably, managers need to be cognizant of waste issues within their factories and across their networks. These vulnerabilities can come in the form of overprocessing or overproduction of delivered inventory, spoilage of raw material after excess time in a warehouse, or resource waste from scrapping defective products. A range of logistics7 issues, ranging from increased warehousing and administrative costs, to improperly or excessively packaged products can result in increased transportation costs.The Cost of Waste
Waste is expensive. High on the list is spoiled inventory, which weighs in at approximately US$163 billion per year8. Another top contender is defective product recalls9, which can, for example, ring up an excess of US$5 billion in costs and incalculable damage to brand reputation and customer loyalty. Pivoting to inventory and inventory management, lack of visibility contributes to inaccurate demand forecasting and insufficient or improper order fulfillment. The latter can travel downstream to negatively affect suppliers, as retailers penalize fulfillment errors10 through chargeback deductions which, in turn, reduce supplier revenue and damage supply chain relationships.The Case for Lean Manufacturing
Manufacturing practices11 like Kaizen, Lean Manufacturing, Six Sigma, and Lean Six Sigma are designed to mitigate waste and improve efficiency and quality. These methodologies have, in one form or another, been adopted by organizations across industries. As a descendant of Kaizen, lean manufacturing12 evolves the Just-In-Time philosophy of leveling factory workflow peaks and valleys and minimizing waste to optimize resources and production flow.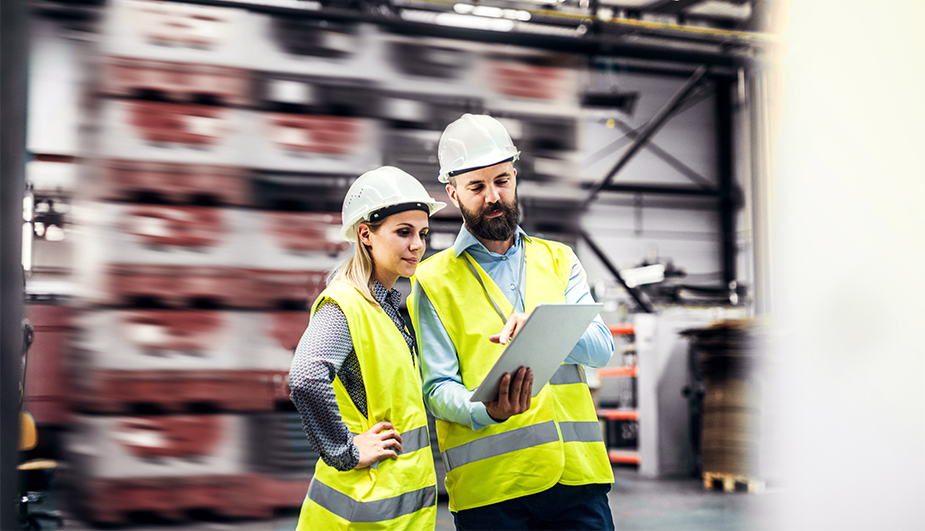
The basic principles13 of lean manufacturing—value, value stream mapping, flow, pull, and perfection—are not specific to any one industry and are instrumental in helping companies to improve their bottom line, increase efficiency, and protect their reputation. Value is defined through the customer lens and is predicated on what the customer is willing to pay for a product or service. The goal of mapping the value stream is to analyze waste and identify improvements across the entire lifecycle of a product. Flow within and among processes can be created once wastes are removed from the value stream. Establishing a pull system entails limiting inventory and work in process while allowing for just-in-time delivery of materials and manufacturing when products are needed. The last principle, perfection, centers on continuous waste reduction and operational improvement.
The Evolution of Lean
From lean’s inception in the early 1900s to “the great enlightenment” of today, the philosophy14 of lean management has remained the same: Put the customer first. Starting with the integration15 of lean management into automotive production by Henry Ford, lean tools and principles have expanded across continents as organizations look to maximize value and profitability through sustainable customer satisfaction and loyalty.
Since the principles of lean manufacturing are centered on eliminating waste and reducing16 cost through streamlined operations, they align well with supply chain management. Supply chain waste represents a broader scope of excess inventory, overproduction, and defective product returns which must be stored, transported, or disposed. It is also excessive energy consumption and emissions that adversely impact the supply chain’s overall environmental footprint. Waste can also come in the form of added expenditures from government and regulatory fines17 that occur when a firm fails to address waste management compliance.
How Lean and Sustainable Principles Work in Tandem for Supply Chain Management
Traditional lean improvements often result in sustainability benefits as a byproduct.18
The Brundtland Report19, aka Our Common Future, was the first recognized report to bring attention to sustainable development in the international forum. Published in 1987, the report highlighted the relationship between society, resources, and the environment, and laid the groundwork for the formation of programs, consortiums, and summits to carry out its detailed directives.
From a truly holistic point of view, sustainability is about doing more with less to meet current needs without compromising future needs. In recent years, sustainable practices have gained attention from and importance20 to governments, investors, and customers. Businesses, in turn, are seeking ways to maximize their resources while minimizing waste, costs, and environmental impact, and to ensure continuous improvement for their long-term viability.
Sustainability stems from efficiency, which stems from lean practices that help reduce waste. Key to this is supply chain visibility. Without it, organizations within are operating in the dark as to where efficiencies can be made and how costs can be reduced.
TrakSYS for Lean Supply Chain Management
Resilient supply chain planning is built on three interdependent pillars: Visibility, scenarios, and master data.21
Companies seeking to employ more efficient manufacturing practices through digitalization of their operations are turning to solutions that make the management of their operations as simple as possible. Parsec’s TrakSYS™ MES is a unified, extensible platform that manages the collection, analysis, and visualization of data for (among other things) lean22 supply chain management. TrakSYS provides the framework to benchmark and manage continuous improvement initiatives by aggregating real-time data to glean insight and control of manufacturing processes and performance. Some of the many TrakSYS features include:
With both preconfigured and customizable solutions, TrakSYS enables the deployment of lean management solutions including 5S, visual management, Kanban, total productive maintenance, and Kaizen.
FAQs
What is Lean Manufacturing?
Lean manufacturing is a system of techniques and activities aimed at maximizing productivity while reducing waste in a manufacturing or service operation.
How do lean principles align with supply chain management optimization?
Lean principles – value, value stream mapping, flow, pull, and perfection – are based on the goal of continuous waste reduction and operational improvement and align with improving the efficiency and performance within a supply chain.
What are the common types of supply chain waste?
The common types of supply chain waste are overproduction of goods, excess time in the production process, unnecessary inventory and transportation of materials or finished goods, additional process steps and movement on the factory floor, process and product defects, and underutilization of workforce talent.
How does lean manufacturing help improve the utilization of raw materials delivered via the supply chain?
Receiving goods on an as-needed basis reduces inventory costs and waste.
How does creating a lean manufacturing production, in turn, create a more sustainable supply chain?
Lean manufacturing streamlines processes, reduces lead times and waste, and boosts profits.
Sources
- Supply-chain resilience: Is there a holy grail? | McKinsey
- Global companies 2021 | Statista
- What Is the Supply Chain? Why Is It Important? | TheStreet
- Risk, resilience, and rebalancing in global value chains | McKinsey
- What is Lean Manufacturing and the 5 Principles Used? | TWI
- Global Supply Chains in a Post-Pandemic World | Harvard Business Review
- How to Reduce Packaging and Logistics Costs | NEFAB
- The Missing Billions: The Real Cost of Supply Chain Waste | Avery Dennison
- Quantifying the Full Costs of a Product Defect | Marsh
- Execution quality: An analysis of fulfillment errors at a retail distribution center | ScienceDirect
- Six Sigma, Kaizen Model or Lean Manufacturing: Which is Best for You? | Formaspace
- What is Lean? Lean Manufacturing & Lean Enterprise | ASQ
- What is Lean Manufacturing and the 5 Principles Used? | TWI
- The Evolution of Lean Thinking – Transitioning from Lean Thinking to FLOW Thinking | InfoQ
- A Brief History of Lean | Lean Enterprise Institute
- How does lean apply throughout the supply chain? | Inchainge
- The importance of minimising waste in the supply chains | Achilles
- A time-tested approach to sustainable manufacturing shows new value | McKinsey
- Brundtland Report | Sustainable Development & Global Environmental Issues | Britannica
- A time-tested approach to sustainable manufacturing shows new value | McKinsey
- Supply chain disruption and resilience | McKinsey
- Lean Management Software | Parsec