Manufacturers are always looking to produce their goods at the highest quality, lowest production cost, and in the least amount of time. Without an innovative, comprehensive digital platform, making those goals a reality becomes needlessly difficult. Through their interoperability, manufacturing execution systems (MES) create a unified flow of information between shop floor automation systems and business level systems, driving improved efficiency and compliance.
Rolling out new technology in a highly complex landscape is rife with challenges, and an inadequate implementation methodology will prevent manufacturers from maximizing the return on investment of their MES solution. As an expert system integrator, you must carefully consider the underlying work processes to determine where the current inefficiencies lie, otherwise you will transfer existing issues from paper to an electronic interface. To maximize value to the client, consider MES implementation as an opportunity to examine processes for improvements. By viewing implementation through this lens, system integrators can come to the table ready to provide value from day one:
1. Overcome Challenges with Integration to Current Technology
When clients invest in new platforms, they want to ensure the technology will integrate with their existing infrastructure, so previous investments are not wasted. Through its extensive interoperability, TrakSYS integrates with ERP software, PLCs, HMIs, scheduling tools, QMS/QIMS systems, CMMS, and more. The platform also integrates with barcode scanners, RFID systems, weighing scales, label printers, warehouse management systems, and a range of communication technologies, which support many internal functionalities. For equipment that doesn’t lend itself to conventional connectivity, the TrakSYS-enabled Smart Devices can be rapidly deployed to obtain real-time values by utilizing an array of off-the-shelf sensors.
2. Avoid Paper on Glass
Many manufacturers still rely on manual, paper-based processes, which hinders efficiency, wastes time, and is prone to human error. Whether manufacturers use pen-and-paper processes for all or some of their steps, MES platforms present an opportunity to transform the plant floor into a truly paperless operation. Take care not to blindly map existing paper processes into the MES. View the implementation as an opportunity to optimize work processes to avoid carrying over inefficiencies. When done properly, siloed data in disparate systems (both on and offline) becomes searchable, actionable, and reportable data and insights.
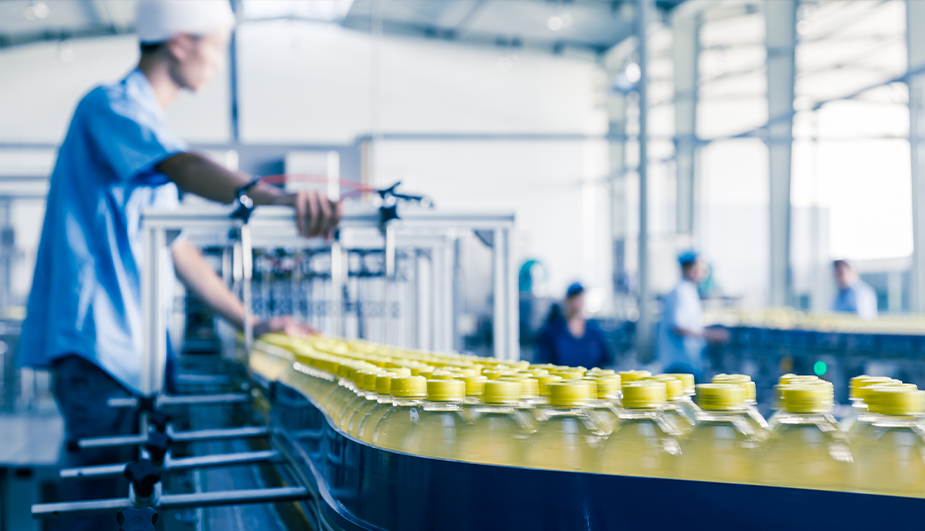
3. Support Lean Warehousing
In today’s manufacturing environment, logistics are tight, and demands on the shop floor drive the need to sync production data with the warehouse. When production and warehousing are connected, the flow of information regarding material movement and finished goods status remains intact. Lean warehousing enables companies to supply the right amount of materials to the point of production, reduce inventory, increase work-in-process visibility, and achieve integrated material flow.
4. Reduce the Impact of Changeovers
By decreasing the time necessary for changeovers through more efficient, leaner processes, businesses can produce more units per day, reduce downtime, and cut production costs. In addition to streamlining and optimizing changeovers, an MES platform ensures changeovers are executed in full, eliminating disruption from halting or restarting the process. For example, the capability of an MES to measure performance data enables manufacturers to deploy lean techniques, such as single-minute exchange of dies (SMED), as a component of a quick changeover. SMED aims to complete as many steps as possible while equipment runs to save time in changeovers when processing the next product.
5. Reduce Waste and Overages
Without real-time visibility into processes, unseen waste can plague shop floor performance. Known as the Hidden Factory, these aspects of a manufacturing process cause quality management issues and reduce overall efficiency. While tracking the number of parts created without an MES is possible, monitoring things like cycle times can be challenging and less accurate, resulting in poor estimates, decreased production goals, and waste. Inventory and warehouse management contribute to hidden waste through spoilage of raw materials, which impacts companies’ purchasing habits.
The Hidden Factory concept evolved to include facets of manufacturing where capacity is tied up, including schedule and availability loss, performance issues, and decreases in quality. These issues can be unlocked with data automation and analysis. Uncovering the Hidden Factory within operations helps manufacturers control scrap and prevent rework.
6. Utility Management, Maintenance, Inventory, and Scheduling
Reduced costs do not only stem from waste reduction. Cost optimization depends on managing every aspect of the manufacturing process, including utility consumption, maintenance, inventory, and scheduling. The increased visibility an MES system provides into the state of operations streamlines the management of these functions, unlocking cost efficiencies.
7. Gain Contextual Visibility into Processes and Streamline Communication
Poor visibility is a destructive force within your organization that leads to supply chain issues. End-to-end visibility helps shorten production lead times, increase on-time delivery percentages, and improve overall operational efficiency. TrakSYS streamlines messaging, alerts, and tasks for the shop floor team by pulling information from disparate systems. In addition to facilitating cross-departmental communication, this shift improves reporting, team member accountability, and process optimization.
With a revolutionary MES platform like TrakSYS, clients can optimize every aspect of their operation. However, these benefits can’t be realized without the attentive assistance of system integrators during the implementation process. Working closely with qualified, experienced system integrators enables clients to rapidly reach greater manufacturing efficiency levels.
To learn more about how partnering with Parsec can help optimize your customers’ manufacturing operation, contact us today.